Читать онлайн Грохочение угля бесплатно
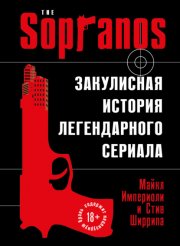
Введение
Все твердые полезные ископаемые в той или иной мере подвергаются классификации по крупности. Из всех способов классификации зернистых материалов, грохочение, как способ разделения частиц по крупности, на просеивающей поверхности занимает важнейшее место в угольной горно-металлургической, строительной, химической и других отраслях промышленности.
Важнейшее место среди подготовительных процессов занимает грохочение в угольной отрасли и, особенно, при обогащении угля. Это связано не только с увеличением пропускной способности углеобогатительных фабрик, но и с внедрением новых обогатительных технологий, для которых выделение и качественная подготовка машинных классов в узких диапазонах крупности является определяющим фактором для эффективной работы этих технологий.
Разработка и использование новых типов грохотов, применение их для классификации шламовых продуктов, особенности оптимизации параметров процессов грохочения в разветвленных схемах углеобогатительных фабрик предопределяет необходимость обобщения результатов работы грохотов и формулировки рекомендаций по их применению.
В данной монографии обобщен опыт применения грохотов для сухого грохочения угля, мокрого грохочения на подвижных грохотах, гидрогрохочения на неподвижной просеивающей поверхности, агрегатной установки гидрогрохотов с инерционными грохотами, гидромеханических грохотах, высокочастотных грохотах и т. д.
Монография может быть полезна для научных работников и специалистов, рабтающих в углеобогатительной отрясли, а также студентов и аспирантов горных вузов, обучающихся по специальности «Обогащение полезных ископаемых».
Глава 1. Общие сведения о грохочении полезных ископаемых
1.1. Назначение и классификация процессов
1.1.1. Основные определения
Горный энциклопедический словарь [1] дает следующее определение процессу грохочения: грохочение – это процесс разделения сыпучего материала по крупности на просеивающих поверхностях.
Устройство для механического разделения (сортирования) сыпучих материалов по крупности кусков (частиц, зерен) путем их грохочения через просеивающую поверхность называется грохотом.
В соответствии с [2] просеивающая поверхность (сито) – это рабочая поверхность грохота, имеющая отверстия (ячейки) конкретного размера и формы. Для круглых отверстий определяющим размером является диаметр, для квадратных – сторона квадрата, для прямоугольных – меньшая сторона прямоугольника, для щелевых – ширина щели.
Материал, поступающий на грохочение, называется исходным, остающийся на просеивающей поверхности – надрешетным (надситным) продуктом, а прошедший через отверстия просеивающей поверхности – подрешетным (подситным) продуктом.
Материал, прошедший через сито с отверстиями d1отв и оставшийся на сите с отверстиями d2отв (d2отв <d1отв), называется классом крупности.
Выход классов крупности (γ) в процентах рассчитывается по формуле
Просеивание сыпучего материала на грохотах осуществляется по т. н. граничной крупности разделения. Под граничной крупностью разделения подразумевается средний диаметр узкого класса крупности, содержание которого в подрешетном и надрешетном продуктах одинаково. Величина граничной крупности разделения может быть больше или меньше характерных размеров отверстий просеивающей поверхности грохота. Она зависит от многих факторов: размера отверстий сита, угла наклона просеивающей поверхности, режимных параметров грохота, гранулометрического состава сыпучего материала, его влажности, формы зерен и т. д.
Граничная крупность разделения определяется по сепарационной характеристике грохота, построенной по данным ситового анализа продуктов грохочения. Исходные данные для построения (в качестве примера) сепарационной характеристики процесса грохочения приведены в табл. 1.1, а определение граничной крупности разделения дано на рис. 1.1.
Таблица 1.1
Исходные данные для построения сепарационной характеристики процесса грохочения
Рис. 1.1. Определение граничной крупности разделения
Построение сепарационной характеристики процесса грохочения осуществляется по извлечению классов крупности в подрешетный продукт (ε(-)) и надрешетный (ε(+)). Проекция точки пересечения этих сепарационных характеристик на ось абсцисс дает значение граничной крупности разделения. В нашем случае ее величина составляет 13,7 мм.
Классы угля, совместно направляемые на обогащение в один аппарат, называют машинным классом.
Классы угля, являющиеся готовыми товарными продуктами, называются сортами.
Шкала грохочения – отношение максимального размера частицы к ее минимальному размеру в каждом классе грохочения, которая может иметь постоянный и непостоянный модули.
Модуль – отношение размеров отверстий смежных решет, сит. В угольной промышленности для стандартных решет (сит) принят модуль
Промышленная шкала грохочения устанавливается в зависимости от обогатимости угля, принятой технологической схемы обогащения, требований потребителей и, как правило, она имеет непостоянный модуль.
При последовательном грохочении материала на п ситах получают п + 1 продукт. В этом случае один из продуктов предыдущего просеивания служит исходным материалом для последующего просеивания.
Размер d наибольших зерен (кусков) подрешетного продукта так же, как и размер наименьших кусков надрешетного продукта, условно принимают равным размеру отверстий сита l, через которое просеивается материал, т. е. d = l. Соответственно обозначают: подрешетный продукт – l (минус l) или – d (минус d); надрешетный продукт + l (плюс l) или +d (плюс d).
Материал, прошедший через сито с отверстиями l1 и оставшийся на сите с отверстиями l2, причем l2< l1, и называется классом крупности. Крупность класса обозначают следующими тремя способами: – l1 +l2 (минус l1, плюс l2) или – d +d; l1-l2 или d1-d2; l2< l1 или d2-d1. Например, классы -25 + 10; 25–10 и 10–25 мм. Из приведенных способов обозначения крупности классов наиболее широко применяют первый и третий, обязательный для использования при грохочении углей (ГОСТ 2093-82) и щебня.
В получаемых при грохочении классах размер наибольших кусков материала d1 всегда меньше размера отверстий сита l1, а размер наименьших кусков d2 – больше отверстий l2. Обозначения крупности классов – d1 +d2 или d1-d2 указывают лишь на то, что данный класс был получен последовательным просеиванием материала на двух ситах с отверстиями размером d1= l1 и d2 = l2.
Извлечение (ε) определяется как отношение количества классов меньше граничной крупности разделения, содержащегося в подрешетном продукте, к его количеству в исходном материале, выраженное в процентах, т. е.
Грохочение зернистых материалов бывает сухим, мокрым и в водной среде.
Сухое грохочение осуществляется без добавления воды. В углеобогащении применяется для предварительного и подготовительного грохочения угля, а также для выделения из рядового угля сухого отсева крупностью 0–6 мм.
Мокрое грохочение осуществляется с добавлением воды. В углеобогащении применяется для подготовительного и тонкого грохочения, соответственно, угля и угольных шламов.
Грохочение в водной среде осуществляется помещением просеивающей поверхности под зеркало воды. В углеобогащении не применяется.
Основным фактором, определяющим применение сухого и мокрого способа подготовки машинных классов, является влажность. Так, по данным ИОТТ, на каждый процент повышения влажности исходного угля сверх 5,5 эффективность грохочения снижается при размере отверстий сит 13 и 6 мм соответственно на 10 и 24 % [19]. Исследованиями ИОТТ установлено, что сухое грохочение мелких классов антрацита по граничному зерну 6 мм при влажности исходного 7–7,5 % невозможно, так как сита при этом полностью залипают.
Таблица 1.2
Динамика изменения влажности углей
В сложившихся условиях, когда влажность антрацита достигает 7–8% (влажность классов 0-13 мм – 9-10 %), а влажность каменных углей приближается к этому значению (табл. 1.2, [11]), необходима разработка эффективных средств интенсификации процессов грохочения.
Трудности, возникающие при грохочении влажного угля, обусловлены проявлениями капиллярного сцепления между отдельными угольными зернами, покрытыми пленкой воды. Под действием сил поверхностного натяжения между пленками воды происходит комкование влажного материала, а в результате действия этих же сил между частицами угля и увлаженной поверхностью сита – залипание сит.
Как показали исследования [27], приведенные на рис. 1.2, влияние сил поверхностного натяжения может быть устранено либо удалением влаги при сушке, либо наполнением промежуточных объемов жидкостью (мокрое грохочение).
Рис. 1.2. Зависимость эффективности грохочения углей (Е) от их влажности (W):
AB – сухое грохочение; BC – грохочение влажного угля; CD – отсутствие грохочения; DF – мокрое грохочение
Силы поверхностного натяжения могут быть уменьшены путей применения поверхностно-активных веществ и увеличения уровня ускорения грохотов.
При сухом грохочении влажных углей увеличение вил разделения достигается путем подбора оптимальных динамических режимов работы грохота и специальных материалов для рабочих поверхности, установкой струнных, консольно-каскадных н других сит, применением центробежных сил, созданием специальных устройств для разрыхления материала. С этой же целью применяются различные устройства и механизмы для очистки рабочей поверхности в вида щеток, самоочищающихся колосников, резиновых шаров и т. п. Однако, несмотря на подобное многообразие средств интенсификация улучшения способов разделения, проблема сухого грохочения влажных углей на современных обогатительных фабриках остается до сих пор не решенной. Во многом это объясняется тем, что при применении электрообогрева сит и средств интенсификации режимов разделения на грохоте, работающем в режиме сухого грохочения, силы, интенсифирующие разделение, действуют, в основном, на просеивающую поверхность, грохота, а не на грохотимый материал, в результате чего не устраняется явление комкования.
В связи в тем, что способы газо- и электрообогрева, а также аэродинамического воздействия на грохотимый материал до этого времени не дали удовлетворительных результатов, наиболее приемлемым методом улучшения классификации углей для условий углеобогатительных фабрик с мокрыми методами обогащения и глубиной до 0 мм, оказалось применение метода мокрого грохочения.
Эффективность указанного способа грохочения объясняется тем обстоятельством, что ликвидация сил капиллярного сцепления между частицами и просеивающей поверхностью грохота осуществляется с помощью внешних импульсов в виде струй воды, одновременно действуя как на грохотимый материал, так и на поверхность грохота.
При влажности материала, превышающей предельное значение (точка D), подвижность зерен возрастает и наступают условия для мокрого грохочения.
При прямом грохочении, когда исходный материал подается на сито, надситный продукт представляет собой частицы не прошедшие через отверстия просеивающей поверхности и обозначается знаком + (плюс), а подситный продукт – частицы, прошедшие через отверстия просеивающей поверхности – обозначается знаком – (минус).
При обратном грохочении, когда исходный материал подается под сито, надситный продукт представляет собой частицы прошедшие через отверстия просеивающей поверхности и обозначается знаком – (минус), а подситный продукт – частицы не прошедшие через отверстия просеивающей поверхности – обозначается со знаком + (плюс).
Просеивание называется сухое дискретное грохочение зернистых материалов, при котором основным интенсифицирующим усилием разделения является сила тяжести. Грохоты, предназначенные для этой операции имеют множество названий, целесообразно их классифицировать как устройство для сухого грохочения.
Гидравлическим грохочением называется мокрое грохочение зернистых материалов, при котором основным интенсифицирующим усилием разделения является сила тяжести. Грохоты, предназначенные для этой операции имеют множество названий, целесообразно их классифицировать как устройства для гидравлического грохочения.
Виброгрохочением называется сухое или мокрое грохочение зернистых материалов, при котором основным интенсифицирующим усилием разделения является сила инерции. Грохоты, предназначенные для этих операций, называются вибрационными грохотами или просто грохотами.
Гидрогрохочением называется мокрое грохочение зернистых материалов в виде пульпы, при котором основным интенсифицирующим усилием разделения является гидродинамическая сила струй воды, вытекающих из сопел. Грохоты, предназначенные для этой операции, называются гидрогрохотами.
Пневмогрохочением называется сухое грохочение зернистых материалов, при котором основным интенсифицирующим усилием разделения является аэродинамическая сила струй воздуха, вытекающих из сопел. Грохоты, предназначенные для этой операции, называются пневмогрохотами.
Пневмогидрогрохочением называется мокрое грохочение зернистых материалов в виде пульпы, при котором основным интенсифицирующим усилием разделения является аэродинамическая сила струй воздуха, вытекающих из сопел. Грохоты, предназначенные для этой операции, называются пневмогидрогрохотами.
Прямоточным грохочением называется грохочение, когда движение надситного продукта совпадает с направлением интенсифицирующего усилия разделения.
Противоточным грохочением называется грохочение. когда движение надситного продукта противоположно направлению интенсифицирующего усилия разделения.
1.1.2. Виды грохочения
Предварительное – для отделения от исходного угля крупных кусков с целью выборки из них породы и других предметов и последующего дробления.
Подготовительное – для получения отдельных (машинных) классов угля, пригодных для раздельного их обогащения или других видов обработки.
Самостоятельное – для выделения сортов сухого отсева.
Контрольное – для контроля крупности готового продукта.
Обесшламливающее – для удаления шлама из машинных классов и продуктов разделения при мокром обогащении.
Обеспыливающее – для удаления шлама из машинных классов и продуктов разделения при сухом обогащении.
Обезвоживающее – для удаления воды от продуктов мокрого обогащения.
Вспомогательное – для выделения мелочи из отдельных сортов.
Избирательное – для получения классов угля, отличающихся не только по крупности, но и качеству.
В практике обогащения углей грохочение осуществляется от крупных кусков к мелким. Верхнее сито имеет отверстия наибольшего, нижнее – наименьшего размера.
1.2. Теоретические основы грохочения
Просеивание зерен нижнего класса сыпучего материала сквозь сито можно рассматривать как операцию, состоящую из двух стадий: зерна нижнего класса должны пройти сквозь слой зерен верхнего класса, чтобы достигнуть поверхности сита; зерна нижнего класса должны пройти через отверстия сита. Осуществлению обеих стадий помогает соответствующий характер движения короба грохота, приводящий слой зерен на сите в разрыхленное состояние и освобождающий сито от зерен, застрявших в его отверстиях.
При встряхивании короба в слое зерен, лежащем на сите, происходит их сегрегация (расслоение по крупности), причем наиболее крупные зерна оказываются в верхнем слое, а наиболее мелкие – на поверхности сита. Последние легко достигают поверхности сита и проходят через его отверстия.
Рис. 1.3. Схема прохождения зерна через квадратное отверстие сита
Зерна проходят через отверстия беспрепятственно, если они не касаются проволоки, т. е. когда центр зерна при падении проектируется на заштрихованную площадь (l – d)2 (рис. 1.3).
Можно считать, что число случаев, благоприятствующих прохождению зерна через отверстие, пропорционально заштрихованной площади (l – d)2, а число всех возможных случаев падения зерна на отверстие пропорционально его площади l2. Вероятность прохождения зерна через отверстие определится отношением площадей:
С учетом толщины проволок сита получено следующее выражение для вероятности прохождения зерна сквозь сито:
Рис. 1.4. Вероятность прохождения зерен через сито в зависимости от их относительного размера
Первый член этого выражения представляет коэффициент живого сечения сита. Следовательно, вероятность прохождения зерна прямо пропорциональна живому сечению сита.
Зерна размером до 0,75l имеют большую вероятность их прохождения через отверстия сита и называются легкогрохотимыми. Небольшое увеличение размера зерен сверх 0,75l предопределяет резкое снижение вероятности прохождения. Поэтому зерна крупностью в пределах от 0,75l до l называются трудногрохотимыми. Зерна диаметром от l до 1,5l называются «затрудняющими», так как они затрудняют просеивание «трудных» зерен. Зерна крупностью более 1,5l существенно не влияют на перемещение «легких» и «трудных» зерен по поверхности сита (рис. 1.4).
Чем больше скорость движения материала по грохоту, тем меньше вероятность просеивания, при прочих равных условиях, и тем больше производительность грохота по исходному материалу.
Сферическое зерно диаметром d (рис. 1.5), движущееся по ситу со скоростью v, пройдет через отверстие при условии, что траектория движения центра его тяжести пересечет верхнюю плоскость сита не дальше точки 01. Если траектория движения зерна пройдет выше, то возможность прохождения его через отверстие маловероятна.
Координаты точки 01
где v – скорость движения зерна, м/с; t – время движения, с; g – ускорение свободного падения, м/с2.
Рис. 1.5. Схема влияния скорости движения зерна на прохождение его через отверстие сита
Из рис. 1.5 следует, что
Из формулы (1.6) видно, что
Подставив в формулу (1.6) значения x1 и t1, получим
Скорость v, при которой обеспечивается прохождение зерна через отверстие,
Для «трудного» зерна размером, приближающимся к размеру отверстия d≈l, получено
где d – размер зерна, м.
Рис. 1.6. Схема влияния наклона и толщины решета на размер зерна, проходящего в отверстие сита
По формуле (1.10) можно вычислить максимальную скорость сферического тела d≈l, при которой обеспечивается беспрепятственное прохождение его через отверстие.
Предельная скорость движения материала (скорость подачи) по формуле (1.10) получена без учета подбрасывания.
При режиме с подбрасыванием скорость движения зерен повышается в 2–3 раза. Оптимальную подачу устанавливают экспериментально в зависимости от производительности и необходимой эффективности грохочения.
Существенное влияние оказывают на процесс грохочения угол наклона и толщина просеивающей поверхности (рис. 1.6). Если грохочение осуществляется на наклонной под углом α плоскости толщиной h, мм, то для определения размера зерна, проходящего через отверстия, получено выражение
Чтобы получить подрешетный продукт одинаковой крупности при α = 20° и, α = 25° размер отверстий наклонного сита должен быть в 1,15 и 1,25 раза больше отверстий горизонтального сита.
В начальный период грохочения эффективность его увеличивается быстро, а затем замедляется. Это объясняется тем, что скорость грохочения зависит от количества зерен, которые должны пройти сквозь отверстия сита. В первые моменты проходят в основном легкогрохотимые зерна, и процесс грохочения протекает быстро. Затем с течением времени количество их становится все меньше и меньше.
Трудногрохотимые же зерна требуют для своего просеивания значительно больше времени. Поэтому и эффективность просеивания с течением времени замедляется.
С увеличением производительности грохота Q, при прочих равных условиях, эффективность грохочения Е понижается.
Таким образом, на эффективность грохочения влияют, в основном, два фактора: гранулометрический состав грохотимого материала и отверстия просеивающей поверхности грохота. На вероятность прохождения частицы через отверстие оказывают влияние технологические, конструктивные, динамические и гидродинамические факторы.
1.3. Гранулометрический состав
1.3.1. Крупность частиц
При дроблении, измельчении и грохочении приходится иметь дело с рыхлыми смесями частиц материалов (породы) различного размера – от максимальных кусков, измеряемых сотнями миллиметров, до мельчайших частиц величиной в несколько микронов.
Куски обычно имеют неправильную форму и их величина может быть охарактеризована лишь несколькими размерами. Для практических целей желательно характеризовать величину отдельного куска одним размером. Этот размер обычно называют «диаметр» куска. Диаметром кусков сферической формы будет диаметр шара. Для кусков кубической формы за диаметр принимают длину ребра куба; для кусков неправильной формы диаметр определяют по главным измерениям – длине l, ширине b и толщине t параллелепипеда, в который вписывается змеряемый кусок. При этом используют все размеры или только некоторые из них. За диаметр d куска принимают:
Перечисленные способы определения диаметра куска неправильной формы используются при изучении отдельных кусков. Формула для вычисления выбирается в зависимости от способа измерений и целей, для которых подсчитывается диаметр куска. С помощью сит можно получить один размер куска. В этом случае приходится пользоваться формулой (а). С помощью микроскопа определяется два размера и можно пользоваться формулами (б) и (г). Для крупных кусков можно получить все три размера и применить формулы (в), (д), (е) и (ж), если надо характеризовать линейный размер, объем, поверхность или удельную поверхность соответственно.
При грохочении, для массовых определений размера зерен, за диаметр зерна принимают размер наименьшего квадратного отверстия, через которое это зерно может проходить.
Крупность всей массы сыпучего материала оценивают по содержанию в ней классов определенной крупности, т. е. по ее гранулометрическому составу. Гранулометрический состав материала определяют посредством анализов:
1) ситового – путем рассева на ситах на классы крупности, для материалов крупнее 0,04 мм;
2) седиментационного – путем разделения материала на фракции по скоростям падения частиц в жидкой среде, для материалов крупностью от 50 до 5 мк;
3) микроскопического – путем измерения частиц под микроскопом и классификации их на группы в узких границах определенных размеров для материалов крупностью менее 50 до десятых долей микрона.
Гранулометрический состав материалов для контроля процессов грохочения, дробления и измельчения на обогатительных фабриках определяют чаще всего посредством ситового анализа.
Средний диаметр частиц определенного класса крупности находится по формуле
Для нескольких классов или всей смеси частиц средний диаметр определяется как среднединамический диаметр по формуле
Выход отдельных классов определяется в процентах. Размер крупных и мелких частиц выражается в миллиметрах, а тонких – в микронах.
Номинальным называют размер квадратной ячейки контрольного сита, через которое проходит 95 % пробы материала. Для оценки номинального диаметра помимо прямых измерений используется поведение частицы в некоторых специфических условиях, например осаждение в воде. Некоторые из наиболее известных номинальных диаметров [3] приведены в табл. 1.3.
Очевидно, что полученный диаметр для частицы неправильной формы будет зависеть от используемой методики измерения. Например, диаметр Стокса dСт определяется при ламинарных условиях потока и не применим при турбулентных потоках, так как в последнем случае частица ориентируется так, чтобы обеспечить максимальное торможение, в то время как в первом случае она ориентируется случайным образом. Поэтому всякий раз при упоминании крупности частиц следует указывать, какой номинальный диаметр используется.
Крупность всей массы сыпучего материала оценивают по содержанию в ней классов определенной крупности, т. е. по ее гранулометрическому составу. Гранулометрический состав материала в зависимости от крупности определяют одним из следующих способов, мК [3]:
Таблица 1.3
Номинальные диаметры
Наиболее часто для контроля процессов грохочения, дробления и измельчения на обогатительных фабриках применяют ситовый анализ.
Для оперативного контроля гранулометрического состава материалов на потоке используют различные конструкции автоматических гранулометров [4]. По принципу действия гранулометры разделяют на ситовые, седиментационные, ультразвуковые, лазерные, оптические и т. д. Гранулометры осуществляют контроль одного (определяющего) либо нескольких классов крупности.
1.3.2. Ситовый анализ
Рассев сыпучего материала с целью определения его гранулометрического состава называется ситовым анализом.
Для рассева применяют набор проволочных сит с квадратными отверстиями.
Последовательный ряд размеров отверстий сит (от больших к меньшим), применяемых для ситового анализа, называется шкалой классификации, а постоянное отношение размеров отверстий смежных сит – модулем шкалы.
Материал крупнее 25 мм рассеивается на качающихся горизонтальных грохотах и ручных ситах, а мельче 25 мм – на лабораторных ситах. Сетка лабораторного сита натянута на цилиндрическую обечайку диаметром 200 мм высотой 50 мм. В верхнюю кромку обечайки, для придания ей жесткости, закатано проволочное кольцо. Нижняя кромка обечайки имеет несколько меньший диаметр, чем верхняя, что позволяет набирать комплекты сит, вставляя их одно в другое, и одновременно вести рассев материала на нескольких ситах. Верхнее сито закрывается крышкой, а нижнее вставляется в чашку-поддон, куда собирается подситный продукт последнего сита.
Масса пробы для ситового анализа принимается в зависимости от крупности наибольшего куска в пробе
Пробы рассеивают сухим или мокрым способом в зависимости от крупности материала и необходимой точности ситового анализа. Если не требуется особой точности и материал не слипающийся, то применяют сухой способ рассева. Сита устанавливают сверху вниз от крупных размеров отверстий к мелким. Пробу засыпают на верхнее сито и весь набор сит встряхивают на механическом встряхивателе в течение 10–30 мин. Затем сита снимают по одному и проверяют качество рассева просеиванием материала вручную. Если за 1 мин контрольного просеивания материала через сито проходит менее 1 % его остатка на сите, то рассев считается законченным. Остаток на каждом сите взвешивается с точностью до 0,01 г на технических весах. Сумма весов всех полученных классов не должна расходиться более чем на 1 % с весом исходной пробы. Если это условие выдерживается, то сумму весов всех классов принимают за 100 %. Выход классов получают делением веса каждого класса на общий их вес. Вычисление ведут до первого десятичного знака.
При наличии в пробе значительного количества мелкого материала и необходимости повышенной точности анализа пробу рассеивают мокрым способом. Пробу засыпают на сито с отверстиями наименьшего размера, например 0,074 мм, и отмывают от нее мельчайшие частиц (шлам) слабой струей воды или погружая сито в бак с водой. Промывку ведут до тех пор, пока промывочная вода не станет прозрачной. Остаток на сите высушивают, взвешивают и по разности весов определяют вес отмытого шлама. Высушенный остаток рассеивают сухим способом на ситах, включая и самое мелкое, на котором отмывался шлам. Подситный продукт этого последнего сита прибавляют к полученному ранее весу отмытого шлама.
Результаты ситового анализа записывают в таблицу, подобную табл.1.4. Вычисляют суммарные выхода, представляющие сумму выходов всех классов крупнее (суммарный выход по плюсу) и мельче (суммарный выход по минусу) отверстий данного сита.
Рис. 1.7. Набор сит для мокрого ситового анализа с орошением
1 – сито; 2 – обечайка сита; 3 – форсунка с брызгалом
Таблица 1.4
Результаты ситового анализа (для примера)
Для ситового анализа применяют встряхиватели сит разных конструкций. В отечественных лабораториях наиболее распространены механические и вибрационные встряхиватели, сообщающие набору (колонке) сит круговые качания в горизонтальной плоскости и удары по крышке набора (встряхивания). Механические встряхиватели постепенно вытесняются более совершенными и простыми электромагнитными вибрационными встряхивателями, которые имеют регулируемую частоту и амплитуду вибраций. Например, встряхивающий аппарат Фрич может устанавливаться на частоту 3000 мин-1 при амплитуде вертикальных колебаний до 3 мм или на 6000 мин-1 при амплитуде 0,5 мм. Для предотвращения резонансных колебаний сеток сит при режиме 3000 мин-1 предусмотрено автоматическое прерывание вибраций на 0,5 с через каждые 3-10 с. Частота 6000 мин-1 применяется при мокром просеивании на микроситах, рабочие поверхности которых имеют отверстия до 5 мкм. Для мокрого просеивания на встряхивателе трудно просеваемых комкующихся материалов разработаны крышки, сита и поддоны. К колонке сит можно прикрепить форсунки-брызгала и подвести воду (рис. 1.7).
Для точных анализов очень тонкой пыли применяют микросита, рабочая поверхность которых представляет собой никелевую фольгу с квадратными отверстиями, расширяющимися вниз. Такие сетки изготовляются электрогальваническим и электродуговым способами или травлением. Точность размера отверстий в микроситах значительно выше, чем в тканых сетках; отклонение от номинального размера составляет ± 2 мкм. Рабочая поверхность оправляется в массивный обод из нержавеющей стали; эффективный диаметр сита 110 мм. Изготовляют микросита с отверстиями размером от 5 до 100 мкм с интервалами 5 или 10 мкм. Живое сечение для сетки с отверстиями размером 5; 10 и 40 мкм составляет соответственно 6,25; 16 и 25 %. На ситах с отверстиями размером 25 мкм возможно сухое просеивание, но чаще микросита применяют при мокром рассеве. Просеивание ведется в жидкостном столбе, т. е. в крышку набора сит подводится вода, которая заполняет их и отводится от поддона. Это предохраняет сита от повреждений и исключает задержку прохождения воды через сетку вследствие действия сил поверхностного натяжения. Навеска материала для анализа равна 1–3 г (1–2 см3). Сита после анализа очищаются в ультразвуковой ванне.
Полную механизацию и автоматизацию трудоемких операций ситового анализа можно обеспечить в случае применения роботов. Так, электронный робот RPS-75 (рис. 1.8) для рассева [3], основанный на использовании акустических колебаний набора из шести сит, обеспечивает анализ смесей от 5000 до 5 мкм. Все операции, начиная от установки сит и кончая расчетом и выдачей результатов на печатающее устройство, механизированы и автоматизированы.
Для автоматического контроля крупности частиц широкое применение получили пульповые гранулометры, работающие на потоке. Ультразвуковой гранулометр PSI-200 фирмы «Оутокумпу (OUTOKUMPU)» с 1992 г. является лидером рынка (по всему миру установлено свыше 300 анализаторов); позволяет определять заданную крупность частиц в необходимом диапазоне. Лазерный гранулометр PSI-500 той же фирмы имеет возможность определять полное распределение частиц по крупности одновременно в трех потоках в диапазоне размеров частиц 1-500 мкм. Из отечественных разработок следует отметить гранулометр ПИК-074 фирмы Союзцветметавтоматика.
Рис. 1.8. Робот-устройство для рассева
1 – электронные весы; 2 – механизм просеивания; 3 – робот-руки; 4 – устройство управления и вычисления (центральный процессор); 5 – печатающее устройство; 6 – координатный графопостроитель; 7 – механизм робота
1.3.3. Характеристики крупности
Характеристикой крупности называется графическое изображение гранулометрического состава сыпучего материала.
Характеристики крупности строят в прямоугольной системе координат: частные – по выходам отдельных классов и суммарные (кумулятивные) – по суммарным выходам классов. При построении частной характеристики по оси абсцисс откладывают величины отверстий сит, применявшихся при ситовом анализе, а по оси ординат – выхода соответствующих классов в процентах. Ординаты, определяющие выхода отдельных классов, строят на меньшем или на большем из диаметров, ограничивающих данный класс, или на диаметре, равном среднеарифметической величине двух крайних диаметров. Полученные точки соединяют прямыми линиями.
По выходам отдельных классов можно также построить график, называемый в статистике столбиковой диаграммой. Последняя составляется из прямоугольников, высота которых пропорциональна выходам классов, а основанием служит интервал крупности классов. Пример построения частной характеристики крупности по выходам отдельных классов и столбиковая диаграмма (по данным табл. 1.4) показана на рис. 1.9, а.
Суммарную характеристику крупности строят как обыкновенную кривую y=f(d), т. е. по точкам, положение которых находят по абсциссам d – диаметрам кусков и ординатам γ – суммарная выходам мельче или крупнее d.
Если по оси ординат откладываются выхода материала крупнее данного диаметра, то характеристика построена «по плюс d». Если же откладываются выхода материала мельче данного диаметра, то характеристика построена «по минус d». Обе кривые характеристик зеркально отражают одна другую и, будучи построены на одном графике, пересекаются в точке, соответствующей выходу материала в 50 %. Пример построения суммарных характеристик показан на рис. 1.9, б. Выход какого-либо класса (-d1 + d2) по суммарной характеристике определяется разностью ординат, построенных на диаметрах d1 и d2.
Суммарные характеристики «по плюс d» бывают выпуклыми, вогнутыми и прямолинейными (рис. 1.10). Выпуклая кривая А получается при преобладании в материале крупных зерен, вогнутая Б – при преобладании мелких зерен. прямолинейная В свидетельствует о равномерном распределении в материале зерен по крупности, т. е. на любом участке характеристики на единицу изменения величины диаметра приходится одинаковое по величине изменение суммарного выхода материала.
Рис. 1.9. Характеристики крупности:
а – частная характеристика и столбиковая диаграмма; б – суммарные характеристики
Характеристики, показанные на рис. 1.10, разбиты на четыре класса с одинаковым диапазоном изменения крупности в каждом классе, равным 25 мм. Выпуклая кривая А характеризует материал, в котором наибольший выход имеет самый крупный класс (-100 +75 мм). По мере уменьшения крупности уменьшается и выход класса. Наименьший выход имеет самый мелкий класс (-25 +0 мм). В материале при вогнутой характеристике Б наблюдается обратная картина. Прямолинейная характеристика В относится к материалу, в котором все четыре класса имеют одинаковый выход.
Рис. 1.10. Различные формы суммарной характеристики
По виду частной характеристики заключения о распределении в материале крупных кусков и мелких зерен сделать нельзя, так как вид ее зависит от набора сит, применявшихся при ситовом анализе. Изменение шкалы сит меняет и вид частной характеристики.
По кривой суммарной характеристики можно определить выход любого класса крупности. По частной характеристике такие определения сделать нельзя, так как по ней точно определяются только выхода классов, полученных при ситовом анализе. Классы других диапазонов крупности можно определить лишь путем интерполяции, принимая изменение выхода в пределах класса по закону прямой линии, что вносит некоторую ошибку в вычислении. Выхода любых классов по суммарной характеристике определяются без такой ошибки.
При построении суммарных характеристик в широком диапазоне крупностей зерен материала отрезки на оси абсцисс в области мелких классов получаются весьма малого размера, что затрудняет построение и использование характеристик. Приходится строить непомерно большие графики. Чтобы избежать этого недостатка, суммарные характеристики строят в системе координат с полулогарифмической или логарифмической шкалами. Полулогарифмическая суммарная характеристика крупности строится в системе координат (lg x; y), где x=1 – размер отверстий сита, γ – суммарный выход классов.
Преимущество полулогарифмической кривой, по сравнению с обыкновенной кривой y=f(d), состоит в том, что расстояния между соседними значениями величин отверстий сит на оси абсцисс в области мелких зерен увеличиваются, а в области крупных – сокращаются, что позволяет правильно отсчитывать выхода мелких классов при обычном размере графика.
Если набор сит, применяемых для ситового анализа, имеет постоянный модуль, то построение полулогарифмической характеристики значительно упрощается, так как отрезки на оси абсцисс будут одинаковой величины. Например, для ряда сит с постоянным модулем М разница между логарифмами размеров смежных сит составит:
Каждый отрезок на оси абсцисс между соседними ситами равен lgM. При построении характеристики за lgM можно принять произвольный отрезок.
Полулогарифмические суммарные характеристики крупности (по данным табл. 1.3) показаны на рис. 1.11. В отличие от обыкновенных кривых суммарной характеристики, левая ветвь полулогарифмических кривых не доходит до ординаты, соответствующей выходу 100 %, так как этому выходу по оси абсцисс соответствует lg0=-∞.
Рис. 1.11. Полулогарифмические суммарные характеристики крупности
Логарифмическая суммарная характеристика крупности строится в системе координат (lgx; lgy), где x=l – размер отверстий сита, y – суммарный выход классов.
Логарифмическая характеристика позволяет, в некоторых случаях, установить наличие закономерности распределения в материале зерен по крупности.
Для дробленных и измельченных мономинеральных пород логарифмическая характеристика, построенная «по минус l», большей частью получается прямолинейной. Пример построения логарифмической суммарной характеристики крупности (по данным табл. 1.3) показан на рис. 1.12.
Рис. 1.12. Логарифмическая суммарная характеристика крупности
1.3.4. Уравнения характеристик крупности
Если логарифмическая суммарная характеристика по минусу прямолинейная, то для такого материала гранулометрический состав можно представить уравнением.
Уравнение прямой линии в логарифмических координатах
Переходя к антилогарифмам, получим
Это уравнение суммарной характеристики, построенной «по минус х», известно под названием уравнения Годэна-Андреева [3].
Величина показателя k определяет направление и степень изгиба кривой характеристики. Если характеристику построить «по плюс x», то она будет: при k>1 – выпуклой, при k=1 – прямой, при k<1 – вогнутой. Следовательно, по величине показателя k можно судить о преобладании в материале крупных или мелких зерен.
Величина параметра А, при данном показателе k, зависит от величины xmax (диаметра максимального зерна материала).
Уравнение характеристики позволяет решать ряд задач, например: определять число зерен в любом классе, поверхность зерен, удельную поверхность и т. п.
Параметры уравнения находятся следующим образом. На логарифмической характеристике выбираются две точки, соответствующие двум наиболее удаленным диаметрам, и определяется показатель k как тангенс угла наклона прямой
Параметр А находится подставкой значения k в уравнение (1.12) для одной из точек.
Если диаметр зерен брать по отношению к диаметру максимального куска в материале, то уравнение Годэна-Андреева преобразуется в «приведенное» уравнение с одним постоянным параметром
или, если y выражено в долях единицы, то
Показатель k находят описанным выше вычислением или, если принять за исходные для расчета x2 и x1=1/2x2, то
Обработка большого количества гранулометрических анализов продуктов дробления и измельчения показала, что во многих случаях лучшее соответствие опытным данным, по сравнению с уравнением Годэна-Андреева, дает уравнение, предложенное Розиным и Раммлером [3]
где R – суммарный выход класса крупнее х (по плюсу), %; x – размер отверстий сита; b и n – параметры, зависящие от свойств материала и размерности величины х.
Соответствие опытных данных уравнению (1.20) можно проверить графическим путем нанесения опытных точек на функциональную координатную систему. При двойном последовательном логарифмировании уравнения (1.20) последнее приобретает вид
Пример построения такого графика (по данным табл. 1.5) показан на рис. 1.13.
Таблица 1.5
Гранулометрический состав исследуемого материала
Рис. 1.13. Характеристика крупности по Розину и Раммлеру
На осях против соответствующих логарифмических величин написаны значения выходов классов и диаметров зерен материала.
Параметры уравнения (1.20) b и n находят по двум известным точкам, решая систему уравнений:
При совместном решении получим
что, впрочем, можно написать и сразу по графику рис. 1.13. Зная n, определяем b:
Для примера по данным табл. 1.5 составлено следующее уравнение характеристики крупности материала:
Таблица 1.6
Уравнения гранулометрических характеристик крупности частиц
Уравнение Розина-Раммлера охватывает опытные точки в широком диапазоне крупностей, но оно не удовлетворяет одному конечному условию: нулевой выход классов достигается только при бесконечно большой крупности материала
При использовании уравнения Розина-Раммлера приходится считаться с этим обстоятельством и принимать конечную крупность материала, соответствующую какому-то определенному значению выхода класса.
В табл. 1.6 приведены наиболее известные уравнения гранулометрических характеристик частиц.
1.3.5. Кривые распределения
Кривые распределения показывают, число частиц или весовые выхода каждого класса крупности в данном материале. Материал, состоящий из смеси частиц разных размеров, разделенный на классы по крупности, можно рассматривать как статический коллектив. Размер частиц будет аргументом коллектива, а общее число частиц в пробе материала или ее общий вес составят числовой или весовой объем статического коллектива. Число частиц в каждом классе или их вес называют численностью класса, частотой или абсолютной частностью, а частоты классов, отнесенные к объему коллектива, – относительными частностями классов.
Если в прямоугольных координатах по оси абсцисс откладывать крупность классов и на соответствующих интервалах крупности построить прямоугольники, площади которых будут пропорциональны частоте класса, то получим гистограмму распределения зерен материала.
Это равнозначно построению прямоугольников высотой, равной частности на единицу длины интервала, на интервале, как основании прямоугольника. При уменьшающемся интервале ступенчатая линия, сверху ограничивающая прямоугольники, приближается к плавной кривой и в пределе дает кривую распределения (рис. 1.14). Ординаты кривой распределения выражают частность на единицу длины бесконечно узкого интервала по оси абсцисс, а площадь под кривой определяет число объектов (число частиц, весовой выход их) в соответствующих промежутках.
Рис. 1.14. Кривая распределения по числу частиц
Таким образом, для построения кривой распределения по числу частиц следует по оси абсцисс на интервале xn-xn-1 построить прямоугольник высотой
Затем построить прямоугольники для всех других классов и соединить кривой точки на серединах верхних сторон прямоугольников. Относительное число частиц в бесконечно малом интервале dx будет
и в классе xn-xn-1
Аналогично строится кривая распределения частностей весовых выходов. Кривые распределения дают более наглядное представление о гранулометрическом составе сыпучих материалов в сравнении с суммарными характеристиками крупности. В классах с наибольшим выходом кривая показывает максимум, а при отсутствии в материале частиц какого-либо размера – падает до нуля. Выхода класса на кривой распределения пропорциональны площадям, ограниченным кривой и двумя ординатами, проведенными на диаметрах, ограничивающих данный класс.
Кривые распределения и суммарной характеристики крупности полностью характеризуют гранулометрический состав материала с точки зрения математической статистики. Возможен аналитический переход от одной кривой к другой, если известно уравнение какой-либо из них.
1.3.6. Вычисление поверхности и числа частиц по уравнениям суммарной характеристики крупности
Если известно уравнение суммарной характеристики крупности, то общий ход вычисления поверхности и числа частиц может быть принят следующий.
Пусть уравнение характеристики «по минусу» будет
где y – выход частиц меньше диаметра x, см.
В 1 г материала с плотностью δ г/см3 объем элементарного класса составит
Для одной частицы кубической формы объем равен x3, а поверхность 6x2.
Число частиц в элементарном классе
а поверхность частиц
Число частиц и их поверхность в классе мельче x2 и крупнее x1 находятся интегрированием этих выражений в пределах от x1 до x2
При вычислении поверхности безразлично, будет ли принята форма частиц за куб или за шар. В самом деле, если принять все частицы шарообразной формы, то получим
Уравнение Розина-Раммлера для суммарной характеристики крупности «по минусу»
где y – суммарный выход класса минус x мк в долях единицы, остальные обозначения см. формулу (1.20).
Уравнение кривой распределения
Число частиц в бесконечно узком классе, содержащемся в 1 г материала,
Поверхность частиц бесконечно узкого класса, содержащегося в 1 г материала,
Общая поверхность частиц в классе – x2+x1, содержащемся в 1 г материала,
После подстановки в уравнение (1.40) получим
В пределах крупности от x2=xm до x1=1 мк вычисленная поверхность относится к классу крупности – xm+1, содержащемуся в 1 г материала, и, следовательно, поверхность классов крупнее xm и мельче 1 мк не учитывается, что вносит некоторую ошибку в расчет.
Выход класса -1 мк составит
Для расчетов xm принимают исходя из выхода класса, равного 0,1 %, т. е.
Число кубических частиц класса – x2+x1 в 1 г пробы по формуле (1.37) будет равно
Уравнение Годэна-Андреева суммарной характеристики крупности «по минусу»
где y– суммарный выход класса минус x мк, в долях единицы; xm – максимальный размер зерна (мк), теоретически соответствующий выходу y=1; k– коэффициент, равный тангенсу угла наклона прямой суммарной характеристики по минусу в логарифмических координатах.
Уравнение кривой распределения
Число зерен в бесконечно узком классе, содержащемся в 1 г материала,
Поверхность частиц бесконечно узкого класса, содержащегося в 1 г материала,
Общая поверхность частиц в классе – x2+x1, содержащемся в 1 г материала,
Число частиц в классе – x2+x1, содержащемся в 1 г материала,
Поверхность и число частиц вычисляются по уравнению суммарной характеристики крупности при некоторых допущениях, вследствие чего расчетные показатели отличаются от действительных и могут быть использованы лишь для целей сравнения.
Основные условности, принимаемые в расчетах:
1) недостаточно обоснованно назначается предельная минимальная крупность частиц; некоторые исследователи считают, что мельчайшие частицы, получаемые при измельчении материала, не должны быть мельче 5-10 Å (1 ангстрем, обозначаемый 1 Å, равен 10-7 мм), что соответствует размеру элементарного кристалла кварца, другие полагают возможным принять за размер мельчайшей частицы 0,1 или 1 мк, учитывая малую вероятность измельчения более мелких частиц;
2) форма частиц принимается за куб или шар; действительная форма частиц отличается от правильной и для различных материалов и крупностей классов поправка на форму частиц оказывается разной.
При измерении поверхности частиц некоторых материалов газоадсорбционным методом получены отношения измеренной поверхности к теоретически вычисленной по среднему диаметру частиц, принятых за шары (табл. 1.7). На основании этих измерений при вычислении поверхности частиц мельче 0,1 мм рекомендуется принимать поправочный коэффициент 1,75 в пределах колебаний 1,3–2,6. Для угольных порошков – коэффициент 1,75 в пределах колебаний 1,6–2,0 [5];
Таблица 1.7
Значение коэффициента, учитывающего форму частиц различных материалов при вычислении их поверхности
3) при вычислении по уравнению Розина-Раммлера приходится условно назначать максимальную крупность частиц, так как соответствующая кривая имеет бесконечную ветвь и нулевой выход соответствует бесконечной крупности частицы;
4) по всему ряду крупности для материала принимается постоянная плотность.
1.3.7. Исчисление среднего диаметра частиц сыпучего материала
Сыпучий материал, состоящий из смеси частиц разных размеров, можно рассматривать, как некоторый статистический коллектив. Средний диаметр смеси частиц, как и всякое среднее, определяется по правилам математической статистики. Средний аргумент x, по рассматриваемому определяющему свойству, коллектива S называют одинаковое для всех членов коллектива значение аргумента x, которое им можно придать, не изменяя определяющего свойства коллектива.
Для отображения определяющего свойства в среднем диаметре необходимо, чтобы усредненный коллектив со средней величиной аргумента x=D1,D2…Dn в отношении этого свойства ничем не отличался от эмпирического x=d1,d2…dn. Если точно установлено определяющее свойство, которое необходимо сохранить при усреднении, то принципиально задача определения среднего диаметра частиц решается просто: выбранное определяющее свойство выражают функцией f(d) переменного от класса к классу диаметра частиц d и той же функцией f(D) искомого среднего диаметра частиц D, который является величиной, постоянной для всех классов.
Определяющее свойство при усреднении должно остаться неизменным, следовательно,
Решая это исходное уравнение относительно D, получаем надлежащую для данного конкретного случая формулу исчисления среднего диаметра.
Обозначим через: w – весовой выход класса, n – число частиц в классе, d – средний диаметр частиц класса, D – средний диаметр частиц всей смеси. Если диапазон изменения крупности частиц в пределах класса достаточно узкий и модуль классификации не превышает 1,414, то с достаточной точностью можно принять
где d1 и d2 – диаметры частиц, ограничивающих класс. Примем для простоты вычислений, что все частицы имеют правильную кубическую форму и одинаковую плотность, тогда
где δ – плотность частиц (постоянная по всем классам при мономинеральном материале).
Рассмотрим на примерах вывод формул среднего диаметра с сохранением определяющего свойства при усреднении.
а) По числовому распределению частиц. Объем коллектива – число всех частиц Σn. Предположим, что определяющим свойством является поверхность всех частиц:
для реальной смеси
для усредненной смеси
Должно существовать равенство
Откуда средний диаметр, обеспечивающий сохранение при усреднении поверхности всех частиц будет исчисляться по формуле
т. е. как среднее квадратичное, взвешенное по числу частиц.
б) По весовому распределению частиц. Объем коллектива – вес всех частиц Σw. Определяющее свойство остается то же самое – поверхность всех частиц:
для реальной смеси
для усредненной смеси
Должно существовать равенство
откуда
т. е. средний диаметр исчисляется как среднее гармоничное, взвешенное по весовым выходам классов.
1.3.8. Порозность материала и его гранпараметр
Пористостью материала называется отношение объема твердой части частицы материала к объему, занимаемому частицей [2].
Пористость является физической характеристикой твердого тела.
Порозностью материала называется отношение объема пустот между частицами материала к объему, занимаемому материалом [6].
Порозность является характеристикой сыпучего материала, указывает на степень удаления частиц друг от друга и зависит от гранулометрического состава материала и способа укладки частиц.
Порозность определяется по уравнению [6]
где m – порозность в долях единицы; α,γ – углы пространственного элемента (рис. 1.15).
На рис. 1.15 показаны виды укладки частиц шарообразной формы, а в табл. 1.8 приведена их характеристика [7].
Формула (1.64) показывает, что порозность материала, состоящая из частиц одинакового размера, не зависит от диаметра последних, а зависит лишь от вида укладки и может изменяться от 0,259 до 0,476.
Таблица 1.8
Характеристика видов укладки шарообразных частиц
Рис. 1.15. Типы укладок слоя шаров:
а – кубическая; б – ромбическая; в – биромбическая; г – тетраоктаэдрическая; д – тетраоктаэдрической укладки; е – октаэдрическая укладка.
В табл. 1.9 приведены результаты определения порозности моноклассов различных материалов по данным [6].
В практике наиболее простым и достоверным [11] методом определения порозности является метод, при котором порозность определяется через насыпную массу виброуплотненного материала, и плотность частиц материала по формуле
где γн – насыпная масса материала в виброуплотненном состоянии, кг/м3; δ – плотность частиц материала, кг/м3.
Естественно, наиболее устойчивая форма укладки октаэдрическая, для которой порозность равна 0,259. При этой геометрии шары имеют наибольшее количество точек соприкосновения, обеспечивающих их поддержку со всех сторон. В то же время кубическая и все промежуточные формы укладок менее устойчивы. Очевидно, что при любом сотрясении частицы будут стремиться занять наиболее устойчивую форму укладки, при которой порозность будет наименьшей. Однако при размещении большого количества частиц потребуется высокое совершенство укладки отдельных единиц, чего нельзя получить в естественных условиях. В естественных условиях следует ожидать образование групп, в которых размещение частиц будет беспорядочным и, где порозность будет иметь величину большую, чем 0,259.
Таблица 1.9
Значения порозности материалов после их виброуплотнения
Для моноклассов различных зернистых материалов следует ожидать, что их порозность будет находиться между теоретическими значениями 0,26 и 0,48.
Полидисперсные материалы обладают меньшей порозностью, чем отдельные классы этого материала. Это объясняется тем, что меньшие по размеру частицы заполняют пространство между большими, тем самым уменьшают объем межчастичных пустот.
Из формулы (1.65) следует, что насыпная масса материала тем больше, чем меньше его порозность. Этим и определяется важность изучения порозности материалов при подготовке шихты к коксованию, при подготовке заполнителей бетона, для асфальтодорожного покрытия.
Данные табл. 1.8 показывают, что порозность различных моноклассов одного и того же материала не зависит от диаметра частиц и практически одинакова. При этом полученные величины порозности находятся в пределах теоретических значений. Различие в порозности между различными материалами – углем, породой, песком – объясняются различной формой частиц (коэффициент формы соответственно равен 0,57; 0,55 и 0,74. Моноклассы материалов, частицы которых более округлы, например, песка, укладываются наиболее плотно, в результате чего величина порозности таких материалов ниже, чем у материалов с угловатыми формами частиц.
Таким образом, для многих отраслей промышленности ставится задача минимизации порозности при составлении искусственных смесей зернистых материалов.
Определим количественное соотношение классов в двойной смеси угля для достижения минимальной порозности (двойная смесь – это смесь из двух моноклассов материала).
Объем, занимаемый первым (крупным) классом
где G1 – масса первого класса, кг; H1 – порозность первого класса.
Объем пустот в первом классе
Объем, занимаемый вторым (мелким) классом
где G2 – масса второго класса, кг; H2 – порозность второго класса.
Для достижения минимальной порозности объем второго класса должен быть равен объему пустот первого класса, т. е.
откуда при одинаковой плотности и порозности частиц
т. е. для получения минимальной порозности двойной смеси количество (мелкого) класса должно быть равно произведению массы первого (крупного) класса на порозность класса.
Выход классов в двойной смеси равен
где H=0,46 – порозность монокласса угля по табл. 1.8.
При добавлении к двойной смеси третьего класса, к тройной смеси четвертого класса и т. д. минимум порозности достается при добавлении последнего класса в том же количестве, что и второго класса в двойной смеси, при этом выход первого класса определяется как
а выхода остальных классов по формуле
где a– выхода классов в долях единицы; n – число классов в смеси; k – порядковый номер класса.
Анализ показывает, что любой угольный материал может быть разделен на две части, из которых первая (крупная) часть является скелетом, с выходом, определяемым по уравнению (1.71), а вторая (мелкая) часть является заполнителем, с выходом, определяемым по формуле (1.72).
Гранулометрическим параметром (гранпараметором) называется отношение средних диаметров скелета и заполнителя, выход которых равен, соответственно, 0,685 и 0,315 [8].
где dc, dз – средневзвешенный диаметр частиц, соответственно, скелета и заполнителя.
Гранулометрический параметр отражает распределение частиц по крупности и связан с коэффициентом распределения – b в уравнении Розина-Раммлера зависимостью, приведенной на рис. 1.16.
Авторами [9] установлена взаимосвязь порозности угольных смесей с их гранпараметром в виде
Гранулометрический параметр является критерием подобия зернистых смесей по плотности укладки их частиц. Все зернистые смеси в сложенном состоянии независимо от их средней крупности, имеющие одинаковый гранулометрический параметр, подобны и имеют одинаковую порозность.
Рис. 1.16. Связь гранпараметра с коэффициентом (-в) в уравнении Розина-Раммлера
1.3.9. Классификация углей по крупности
Класс – это совокупность частиц, крупность которых ограничена размерами отверстий двух смежнорасположенных сит, связанных между собой модулем шкалы классификации.
Сорт – это совокупность частиц, крупность которых ограничена размерами отверстий двух смежнорасположенных сит, связанных или на связанных между собой модулем шкалы классификации, и соответствует техническим условиям на товарную продукцию.
В нашей стране принята следующая классификация сортового угольного топлива [10]:
Машинный класс – это совокупность частиц, крупность которых ограничена размерами двух смежнорасположенных сит, не связанных между собой модулем шкалы классификации, и соответствует технической характеристике обогатительного аппарата.
Предлагается следующая классификация угля по крупности частиц для машинных классов [11]:
1.4. Процесс грохочения
1.4.1. Последовательность выделения классов при грохочении
При грохочении сыпучего материала с выделением более двух классов последовательность выделения их определяется расположением сит.
Различают следующие схемы выделения классов: от крупного класса к мелкому; от мелкого класса к крупному; смешанную или комбинированную.
При грохочении от крупного класса к мелкому сита располагают одно под другим (рис. 1.17, а). Верхнее сито имеет наибольшие отверстия, а книзу размеры отверстий сит уменьшаются. Эта последовательность выделения классов имеет следующие преимущества.
Рис. 1.17. Схемы выделения классов при грохочении:
а, б – от крупного к мелкому; в – от мелкого к крупному; г – смешанная
1. Меньший износ сит, потому что вся масса материала и наибольшие куски поступают на рабочую поверхность с крупными отверстиями, которая обычно собирается из стальных решет и защищает поверхности с мелкими отверстиями из проволочных сеток.
2. Более высокая эффективность грохочения мелких классов, так как на сита с мелкими отверстиями поступает меньшее количество материала.
3. Меньшее крошение крупных кусков при грохочении, так как они быстрее выводятся из процесса. Последнее имеет большое значение для углей.
4. Компактность установки грохочения по занимаемой площади вследствие многоярусного расположения сит.
Из недостатков этой схемы следует отметить неудобства в наблюдении за состоянием нижних сит, затруднения в их замене и скученность разгрузки классов в одном конце грохота. Расположение сит по схеме рис. 1.17, б позволяет рассредоточить места вывода классов. При таком расположении также несколько увеличивается эффективность грохочения на нижнем сите, так как наличие поддона под верхним ситом позволяет направить материал в начало нижнего сита.
При грохочении от мелкого класса к крупному сита располагают последовательно в порядке возрастания величины их отверстий (рис. 1.17, в). Достоинства такой последовательности выделения классов заключаются в удобстве смены сит и наблюдения за их состоянием. Помимо того, разгрузка классов рассредоточена по всей длине сит. Недостатки этой схемы, однако, весьма существенны.
1. Быстрый износ сит и пониженная эффективность грохочения, так как вся масса материала загружается на сито с самыми мелкими отверстиями.
2. Возможность крошения крупных кусков хрупкого материала.
При комбинированной схеме выделения классов сита располагаются частично от крупного к мелкому и частично – от мелкого к крупному (рис. 1.17, г).
В практике чаще применяются схемы выделения классов от крупного к мелкому и комбинированные. При необходимости выделения сухого отсева из рядового угля перед его обогащением применяется схема выделения классов от мелкого к крупному.
1.4.2. Баланс материала при грохочении
На рис. 1.18 приведена схема грохочения и обозначение продуктов.
Рис. 1.18. Схема грохочения
Рассмотрим баланс материала при грохочении
Также имеем
И, Н, П – масса, соответственно, исходного, надрешетного и подрешетного продуктов;
α, β, ϴ – содержание класса меньше крупности разделения, соответственно, в исходном, надрешетном и подрешетном продуктах, %.
Выходом продукта называется отношение его массы к массе исходного продукта (выраженное в процентах). Тогда
Баланс продуктов по выходу
Баланс продуктов по классу меньше крупности разделения
или, разделив на массу исходного продукта,
Пользуясь определением выхода, получим
Баланс продуктов по классу больше крупности разделения
или, разделив на массу исходного продукта,
Пользуясь определением выхода, получим
Извлечением называется отношение массы класса заданной крупности находящегося в продукте разделения к массе этого класса, содержащегося в исходном материале, выраженное в процентах.
Извлечение класса меньше крупности разделения в подрешетный продукт
Подставляя в выражение (1.79) значение γн из выражения (1.78) и преобразуя относительно γп, получим
Подставляя γп из (1.82) в выражение (1.81) окончательно получим
Извлечение класса меньше крупности разделения в надрешетный продукт
Подставляя в выражение (1.79) значение γп из выражения (1.78) и преобразуя относительно γн, получим
Подставляя γн из (1.85) в выражение (1.84) окончательно получим
Извлечение класса больше крупности разделения в надрешетный продукт
или, используя выражение (1.85)
Извлечение класса больше крупности разделения в подрешетный продукт
или, используя выражение (1.82)
Баланс класса меньше крупности разделения по извлечению
Баланс класса больше крупности разделения по извлечению
1.4.3. Эффективность грохочения
Для количественной оценки полноты отделения мелкого материала от крупного при грохочении введено понятие эффективности грохочения.
Эффективностью грохочения называется выраженное в процентах или в долях единицы отношение массы подрешетного продукта к массе нижнего класса в исходном материале.
При отсутствии в подрешетном продукте классов больше крупности разделения, т. е. ϴ=100 %, выражение (1.93) приобретает следующий вид
Рассматривая грохочение как операцию разделения на два продукта, для оценки процесса используют критерии эффективности грохочения (которые ошибочно называют также эффективностью грохочения).
В основу этих критериев положено извлечение соответствующих классов в соответствующие продукты.
Критерий эффективности грохочения по извлечению классов в подрешетный продукт
При ϴ=100 %, выражение (1.95) преобразовывается в уравнение (1.94).
Критерий эффективности грохочения по извлечению соответствующих классов в соответствующие продукты
При ϴ=100 %, выражение (1.96) также преобразовывается в уравнение (1.94).
Критерий эффективности по гранпараметру продуктов разделения [9]
Эффективность грохочения и критерии эффективности грохочения определяются по гранулометрическому составу продуктов разделения.
1.4.4. «Легкие», «трудные» и «затрудняющие» частицы
Просеивание частиц нижнего класса сыпучего материала сквозь сито можно рассматривать состоящим из двух стадий:
1) частицы нижнего класса должны пройти сквозь слой частиц верхнего класса, чтобы достигнуть поверхности сита;
2) частицы нижнего класса должны пройти через отверстия сита.
Осуществлению обеих стадий помогает соответствующий характер движения короба грохота, приводящий слой частиц на сите в разрыхленное состояние и освобождающий сито от частиц, застрявших в его отверстиях.
При встряхивании короба в слое частиц, лежащем на сите, происходит их сегрегация (расслоение по крупности), причем наиболее крупные частицы оказываются в верхнем слое, а наиболее мелкие – на поверхности сита. Последние легко достигают поверхности сита и проходят через его отверстия. Но зерна, близкие по величине к размеру отверстий сита, с трудом проходят в промежутках между более крупными частицами нижнего слоя материала, лежащего на сите, а также и через отверстия сита.
Практика грохочения показала, что частицы, диаметр которых меньше, чем три четверти величины отверстий сита, легко проходят в промежутках между крупными частицами материала на сите и по достижении ими поверхности сита немедленно проваливаются через отверстия. Такие частицы, в отношении их грохотимости, называют «легкими». Частицы крупнее трех четвертей величины отверстий сита проходят с трудом в промежутках между крупными частицами и через отверстия сита. И эта трудность прохождения прогрессивно возрастает по мере приближения диаметра частиц к величине отверстий сита. Такие частицы называют «трудными» [5].
Частицы, диаметр которых больше полуторной величины отверстий сита, не оказывают существенного влияния на перемещение «легких» и «трудных» частиц к поверхности сита. Но нижний слой материала на сите, состоящий из частиц диаметром меньше полуторной величины отверстий сита, затрудняет проникновение к его поверхности близких к ним по величине «трудных» частиц. Кроме того, частицы, близкие по диаметру к величине отверстий сита, но больше их, легко застревают в отверстиях и «заслепляют» сито. Такие частицы, по размеру большие отверстий сита, но меньшие полуторной величины их, называют «затрудняющими».
Чем меньше в исходном материале «трудных» и «затрудняющих» частиц, тем легче его грохочение и тем выше, при прочих равных условиях, эффективность грохочения.
Характеристики крупности легко- и трудногрохотимого материалов на ситах с размером отверстий l показаны на рис. 1.19.
Эффективность грохочения по «трудным» частицам определяется по общей формуле (1.93), где α, β, ϴ – содержания «трудных» частиц соответственно в исходном материале, надрешетном и подрешетном продуктах.
Рис. 1.19. Характеристики крупности:
а – легкогрохотимого материала; б – трудногрохотимого материала
1.4.5. Вероятность прохождения частиц через отверстия сита
Рассмотрим условия прохождения отдельной частицы через отверстия сита. Вероятность р какого-либо события равна отношению числа случаев m, благоприятствующих наступлению данного события, к числу всех возможных случаев n, при которых данное событие может произойти. Причем все случаи должны быть равновозможными и несовместимыми. Следовательно, величина вероятности измеряется отношением
При m=0 имеем p=0 – невозможность, когда ни один случай не благоприятствует наступлению события, при m=n имеем p=1 – достоверность, когда каждый случай благоприятствует событию.
Величина N, обратная вероятности p, определяет вероятное число случаев, при котором данное событие может иметь место
Предположим, что мы имеем сито из бесконечно тонкой проволоки с квадратными отверстиями величиной l. Допустим также, что шарообразные частицы диаметром d при грохочении падают перпендикулярно к плоскости сита. Будем считать, что зерна проходят через отверстия беспрепятственно, если не касаются проволоки, т. е. центр частицы при падении проектируется на заштрихованную площадь (l-d)2 (рис. 1.20, а).
Можно считать, что число случаев, благоприятствующих прохождению зерна через отверстие, пропорционально заштрихованной площади (l-d)2, а число всех возможных случаев падения частицы на отверстие пропорционального его площади l2. Вероятность прохождения зерна через отверстие определится отношением площадей
Тогда величина N, обратная вероятности p, определит вероятное число отверстий, которое необходимо встретить частице, чтобы в одно из них пройти сквозь сито.
Рис. 1.20. Схема прохождения частицы через отверстие сита
Значения величин p и N для различных отношений d/l приведены в табл. 1.10, по данным которой построен график (рис. 1.21). Из графика видно, что небольшое увеличение диаметра частицы сверх 0,75l вызывает значительное возрастание числа отверстий для прохождения частицы сквозь сито.
Таблица 1.10
Вероятность прохождения зерна через отверстие в зависимости от его относительного размера
Следовательно, теория вероятностей подтверждает принятое практикой деление частиц на «легкие» (d<0,75l) и «трудные» (d>0,75l).
Если учесть толщину проволок сита (рис. 1.20, б), то, рассуждая аналогично предыдущему, получим следующее выражение для вероятности прохождения частицы сквозь сито:
Первый член этого выражения – коэффициент живого сечения сита. Отсюда видно, что вероятность прохождения частицы прямо пропорциональна живому сечению сита.
На основе рассмотренного определения вероятности прохождения частиц сквозь сито можно установить эффективность грохочения частиц диаметром x=d/l (весьма узкого класса).
Согласно формуле (1.101) имеем
где L – коэффициент живого сечения сита в долях единицы.
Рис. 1.21. Вероятность прохождения частицы сквозь сито в зависимости от относительного его размера
Число отверстий N, которое надо встретить частицам, составляющим рассматриваемый узкий класс, для полного прохождения сквозь сито, равно
Встреча с этим числом отверстий обеспечивается при определенной продолжительности грохочения t. Если время грохочения t1 меньше t, то частицы просеваемого узкого класса встретят число отверстий N1, меньшее N, и пройдут сквозь сито не полностью. Извлечение этого узкого класса в подрешетный продукт (эффективность грохочения по данному классу)
где C – постоянный для данного грохота коэффициент пропорциональности.
Для приближенных подсчетов можно пользоваться эмпирической формулой
где a – параметр, являющийся некоторой функцией времени грохочения.
1.5. Классификация грохотов
В практике грохочения сыпучих материалов применяются грохоты различных конструкций. Детальная их классификация по общим конструктивным признакам, по характеру движения просеивающей поверхности и ее элементов или по типу приводного механизма, обеспечивающего характер движения, получается громоздкой и затруднительной.
Поэтому для систематизированного описания грохотов предлагается ограничиться подразделением их на следующие группы:
– неподвижные (группа I);
– валковые (группа II);
– барабанные (группа III);
– плоские качающиеся (группа IV);
– полувибрационные (группа V);
– вибрационные с круговыми и прямолинейными колебаниями (групп VI);
– гидрогрохоты (группа VII);
– гидромеханические грохоты (группа VIII);
– грохоты с упруго-деформирующей поверхностью (группа IХ);
– специальные (группа Х).
Условно различные типы серийно выпускаемых грохотов обозначают буквами и цифрами.
Начальная буква Г обозначает тип машины – грохот; следующая (или следующие) обозначают исполнение грохота по принципу действия:
Г – гидрогрохот, И – инерционные с круговыми или близкими к ним колебаниями, С – самобалансный с прямолинейными колебаниями, ИС – самобалансный с колебаниями близкими к прямолинейным, Р – резонансный, К – качающийся; предпоследняя буква может обозначать исполнение грохота по принципу геометрии просеивающей поверхности; Ц – цилиндрический, Б – барабанный, В – валковый, К – конический, Д – двухкоробковый; последняя буква обозначает исполнение грохота в зависимости от насыпной плотности грохотимого материала: Л – легкий тип, С – средний, Т – тяжелый.
Первая цифра в условном обозначении показывает ширину просеивающей поверхности: 2-1000 мм, 3-1250 мм, 4-1500 мм, 5-1750 мм, 6-2000 мм, 7-2500 мм, 8-3000 мм, 9-3500 мм, 10-4000 мм, вторая – число ярусов (дек) сит.
Обозначение грохота может заканчивается буквенным или цифровым индексом его модификации, например, абривиатура ГИЛ-43 означает, что это грохот инерционный легкого типа с шириною рабочей поверхности 1500 мм с тремя ярусами просеивающей поверхности.
В настоящее время в Украине фирмы, изготавливающие различные типы грохотов, в т. ч. и специальной конструкции, дают им свои обозначения, отличные от общепринятых.
Грохота выпускаются с укрытием (для сухого способа грохочения) и без укрытия (для мокрого способа грохочения).
Вибрационные грохоты характеризуются коэффициентом динамичности
где a – амплитуда колебаний, м; n – число оборотов в мин.; αв.к. – угол наклона направления колебаний вибраций, град.; αППП – угол наклона подвижной просеивающей поверхности к горизонту, град.; g – ускорение свободного падения (9,81 м/с2).
Нами рассматривается классификация грохотов по их назначению, т. е. для:
– сухого грохочения угля;
– мокрого виброгрохочения угля;
– гидрогрохочения угля;
– гидромеханического грохочения угля;
– гидравлического грохочения мелкого угля;
– мокрого виброгрохочения угольного шлама.
1.6. Классификация рабочих поверхностей грохотов
Просеивающие поверхности, применяемые в качестве рабочих поверхностей на грохотах для разделения зернистых материалов по крупности, отличаются друг от друга по материалу, из которого они изготавливаются, по способу изготовления, по назначению и по форме отверстий.
Для изготовления просеивающих поверхностей применяются в основном следующие материалы:
– специализированные стали различных марок;
– резина и полиуретаны;
– капросталь, лавсан и другие полимеры.
По способу изготовления просеивающие поверхности различаются на:
– колосниковые;
– штампованные;
– проволочные плетенные;
– проволочные сварные;
– литые и прессованные;
– тканные.
По форме отверстий просеивающие поверхности различаются на сита с отверстиями:
– квадратными;
– прямоугольными;
– щелевыми;
– фигурными;
– специальной формы.
По назначению просеивающие поверхности предназначены для:
– предварительного грохочения;
– подготовительного грохочения;
– рассортировки материалов;
– грохочения шламовых продуктов;
– ультратонкого грохочения.
Нами рассматривается классификация просеивающих поверхностей по способам изготовления, материалу и назначению:
– штампованные сита (группа I);
– колосниковые наборные сита (группа II);
– плетенные проволочные сита (группа III);
– сварные проволочные сита (группа IV);
– прессованные и литые сита из резины и полиуретана (группа V);
– сита специальные (группа VI);
– технические ткани (группа VII);
– проволочные литые (группа VIII);
– декоративные сита, технические сетки и технические ткани (группа IX).
Глава 2. Грохоты для сухого грохочения угля
2.1. Грохоты неподвижные колосниковые
К этой группе относится грохот колосниковый неподвижный, изображенный на рис. 2.1.
Рис. 2.1. Грохот колосниковый неподвижный:
1 – колосники; 2 – болт стяжной; 3 – трубка распорная
Грохот представляет собой решетку, собранную из колосников, устанавливаемых под углом к горизонту. Материал, загруженный на верхний конец решетки, движется по ней под действием силы тяжести. При этом мелкие классы проваливаются через щели решетки, а крупный класс перемещается к разгрузке грохота.
Грохоты этого типа применяются для крупного грохочения. Размер щели между колосниками от 25 до 100мм. Угол наклона решетки от 30 градусов и выше. Размеры и формы поперечных сечений колосников могут быть разнообразными в зависимости от условий проведения процесса грохочения и требований к его продуктам.
2.2. Грохоты неподвижные струнные
Неподвижные струнные грохоты (сита) применяются на операции сухого отсева в узлах подготовительного грохочения углей.
Неподвижный односитный наклонный грохот состоит из короба, в котором закреплена просеивающая поверхность из проволочных струн, поддона для сбора подрешетного продукта и металлического конуса, сообщающегося с аспирационной системой.
Техническая характеристика струнных грохотов определяется компоновкой оборудования в узлах подготовительного грохочения. Техническая характеристика неподвижного струнного грохота, установленного на ЦОФ «Червоноградская» [12]
Принцип работы струнного грохота. Исходный материал по разгонному желобу со скоростью до 3 м/с поступает на просеивающую поверхность, где под действием гравитационных сил происходит выделение из такого быстродвижущегося слоя зерен меньше 13мм в подрешетный продукт, который собирается в поддон и через отверстия в нем попадает на ленточный конвейер. Надрешетный продукт сходит с рабочей поверхности на ленточный конвейер рядового угля. Подрешетный продукт является сухим отсевом и направляется при необходимости в присадку к мелкому концентрату или, при соответствующей зольности, является самостоятельным товарным продуктом.
2.3. Грохоты неподвижные с принудительной очисткой сит
Грохот струнный крутонаклонный типа ГЛС
Одним из перспективных направлений повышения эффективности грохочения влажных углей является создание машин, рассев материалов в которых осуществляется в тонком быстродвижущемся слое. К ним относятся разработанные ГП «Укрнииуглеобогащение» стационарный крутонаклонный ленточно-струнный грохот с принудительной очисткой просеивающей поверхности (типа ГЛС) [12].
Грохочение сыпучих материалов в тонком быстродвижущемся слое характеризуется тем, что мелкие зерна отсеваемого класса практически мгновенно достигают отверстий сита, влажный материал в меньшей степени комкуется, создаются благоприятные условия для реализации эффекта отсева зерен, меньших по своим размерам, чем отверстия просеивающей поверхности, что дает возможность применять сита с повышенным живым сечением и менее склонных к залипанию.
Испытания и промышленная эксплуатация ленточно-струнных грохотов на углеобогатительных фабриках показали правильность выбранного направления интенсификации рассева углей повышенной влажности за счет самосортирования зерен грохотимого материала в быстронесущем тонком разрыхленном слое с одновременной непрерывной очисткой щелей просеивающей поверхности.
На рис. 2.2 изображен общий вид этого грохота. Его конструкция включает кривошипно-шатунный привод 1, раму грохота 2, раму подвижную 3, раму неподвижную 4, желоб загрузочный 5, устройство тормозное 6, ролик опорный 7, колосниковое верхнее сито 8, опору 9, очистители 10 и струнное сито 11.
Рядовой уголь крупностью до 300 мм подается на разгрузочное колосниковое сито с расходящейся по ходу движения материала щелью. Сито изготавливается из круглых стальных стержней диаметром 40 мм. Для снижения разрушительного воздействия крупных кусков материала над разгрузочным ситом устанавливается тормозное устройство, состоящее из резиновых брусьев квадратного профиля 40×40 мм и металлических цепей.
Подрешетный продукт разгрузочного сита, верхний предел крупности которого около 80 мм, поступает на нижнюю просеивающую поверхность, сформированную из струн круглого профиля диаметром 5 мм. В боковинах неподвижной рамы имеется ряд отверстий, в которых крепятся концы струн. Величина шага отверстий выбирается в зависимости от требуемой граничной крупности разделения. Угол наклона струнной просеивающей поверхности регулируется в диапазоне 48–52° к горизонту, что обеспечивает процесс рассева угля в тонком быстродвижущемся слое.
Рис. 2.2. Общий вид струнного крутонаклонного грохота типа ГЛС
Рис. 2.3. Поперечное сечение крутонаклонноло струнного грохота (схематично)
Для очистки, просеивающей поверхности на подвижной раме установлен ряд очистителей. Из рис. 2.3, где показано поперечное сечение грохота, видно, что очистители установлены по всей ширине просеивающей поверхности, а их отверстия, через которые проходят струны, находятся в одной плоскости с отверстиями боковин неподвижной рамы, в которых закреплены концы струн.
Кривошипно-шатунный привод сообщает подвижной раме и установленным на ней очистителям возвратно-поступа-тельное движение. При этом очистители, проходя через струны, очищают их. Расстояние между очистителями 175 мм, а длина их хода – 200 мм. Использование для изготовления просеивающей поверхности струн круглого профиля позволило значительно упростить конструкцию очистителей, применив съемные пластины из износостойкого полимерного материала, что обеспечит снижение установочной мощности привода грохота и повышение ресурса струн и очистителей из-за уменьшения сил трения между ними.
Результаты экспериментальных исследований процесса грохочения в тонком быстродвижущемся слое, проведенные в ГП «Укрнииуглеобогащение», а также технологические показатели работы крутонаклонных струнных грохотов, накопленные за время их эксплуатации в различных условиях на обогатительных фабриках, перерабатывающих энергетические угли и антрациты, дают основание считать, что эти грохоты способны удовлетворительно отсевать класс (0–6) мм из рядовых углей с производительностью до 350 т/ч и влажностью отсеянного класса до 9 %. При этом извлечение этого класса в подрешетный продукт составляет 40–65 %, а потери зерен угля крупнее 6 мм в отсевах не превышают 5 %.
Грохот скребковый
К грохотам с неподвижным рабочим органом относятся скребковый грохот, разработанный ГП «Укрнииуглеобогащение» совместно с ЦОФ «Киселевская» (Украина), изображенный на рис. 2.4.
Рис. 2.4. Грохот скребковый:
1 – став коробчатый; 2 – просеивающая поверхность; 3 – рыхлители, 4 – боковина става; 5 – цепь тяговая; 6 – скребки; 7 – секция приводная, 8 – днища; 9 – секция натяжная
Грохот предназначен для предварительного отсева мелких классов из влажных рядовых углей и антрацитов по ходу их транспортирования к аппаратам последующих технологических операций.
Просеивающая поверхность грохота формируется из отдельных секций щелевых сеток, жестко установленных в коробчатом ставе под верхней ветвью тяговой цепи. Ширина щелей сеток находится в пределах 3–6 мм в зависимости от граничной крупности разделения. Рыхлители выполнены в виде грабель, верхний конец которых шарнирно крепится к боковинам става, а нижний опирается на просеивающую поверхность.
Посредством скребков исходный рядовой уголь перемещается по щелевой просеивающей поверхности, при этом происходит отсев мелких классов. При контакте зерен угля с зубьями рыхлителей происходит разрушение слипшихся комков, перемешивание и разрыхление потока угля, что интенсифицирует процесс грохочения. Отсеянный подрешетный продукт транспортируется скребками по днищу под нижней ветвью тяговой цепи к разгрузочному проему.
Испытания скребкового грохота в промышленных условиях ЦОФ «Киселевская» показали, что его просеивающая поверхность практически не подвержена залипанию влажными углями. Ее очистка обеспечивается зернами угля с остроугольными выступами, заходящими в конически расширяющиеся щели просеивающей поверхности при транспортировании скребками.
Нагрузка по исходному питанию во время испытаний изменялась от 120 до 320 т/ч. При ширине щели просеивающей поверхности 4 мм граничная крупность разделения составила 6 мм. В исходном рядовом антраците содержание отсеваемого класса (0–6) мм было в пределах 42–54 %, а величина влажности колебалась от 6,8 до 10,1 %. При таких условиях извлечение в подрешетный продукт класса (0–6) мм составляло 43,7-83,2 %, а содержание в отсеве зерен крупные 6 мм не превышало 8,5-11,7 %.
Эти результаты имели место при длине просеивающей поверхности грохота 20,5 м и ширине 1,4 м.
По сравнению с серийно выпускаемыми вибрационными грохотами типа ГИЛ, работающими в аналогичных условиях, на операции сухого подготовительного грохочения грохот скребковый имеет следующие преимущества: просеивающая поверхность практически не залипает, возможен рассев рядовых каменных углей и антрацитов с влажностью класса (0–6) мм до 10 %, отсутствие вибраций, конструкция проста и надежна, высота приемлема для углеобогатительных фабрик, в одной машине совмещены просеивающие и транспортные функции, удобна компоновка в схеме цепи аппаратов предприятий.
Недостатком грохота скребкового является использование в его конструкции дорогостоящей щелевой сетки из легированной стали с малым живым сечением.
Отсутствие вибраций позволяет применять в качестве просеивающей поверхности сварные колосниковые сита или резинометаллические сита с упругой заделкой колосников из износостойкого металла.
Грохот скребковый рекомендуется для работы на операции предварительного отсева мелких классов из грузопотоков рядовых углей повышенной влажности мощностью до 300 т/ч по граничной крупности разделения 6–8 мм. При влажности класса (0–6) мм в исходном питании до 8 % возможно его применение на операции сухого подготовительного грохочения.
2.4. Грохоты валковые
Эти грохоты используются, как правило, для предварительного грохочения с целью выделения продукта меньше 50-150 мм из грузопотока крупнокускового материала с верхним пределом крупности до 500 мм.
На буроугольных брикетных фабриках валковые грохоты со щелью 5–6 мм применяются на операции подготовительного грохочения.
Валковые грохоты состоят из ряда параллельных валков, установленных на наклонной раме и вращающихся в направлении движения материала. На валки насажены или отлиты заодно с ними диски. Форма дисков может быть круглой или фигурной, например, в виде «сферического» треугольника, стороны которого описаны дугами окружности. Круглые диски могут быть установлены центрично или эксцентрично.
Валки образуют просеивающую поверхность с отверстиями, форма и размеры которых определяются расстоянием между валками и формой дисков.
Рис. 2.5. Общий вид валкового грохота с эксцентричными дисками
На рис. 2.5 изображен общий вид валкового грохота с эксцентричными дисками. Грохот состоит из рамы 1, короба 2, семи валков 3, вращающихся в подшипниках качения 4, и привода. На валках эксцентрично насажены круглые диски 5. Электродвигатель 6 через упругую муфту, редуктор 7 и цепную передачу 8 приводит во вращение средний валок, от которого через короткие цепные передачи 9, расположенные по одну сторону короба, приводятся во вращение остальные валки.
Перемещение угля вдоль грохота осуществляется эксцентрично расположенными дисками, которые насажены на валках со смещением в 90о . Этим достигается энергичное разрыхление угля на грохоте и повышается эффективность грохочения. Цепная звездочка приводного вала имеет предохранительное устройство в виде шпильки, которая срезается при перегрузке грохота (например, при заклинивании валков).
Двойные звездочки иногда располагаются по обе стороны валков через один, что позволяет получить более равномерную нагрузку на короб и детали грохота.
В зависимости от размера отверстий (50-150 мм) и ширины просеивающей поверхности (1270–1500 мм) производительность грохотов колеблется от 200- до 600 т/ч.
Валковые грохоты отличаются спокойной и надежной работой, обладают большой производительностью и хорошей эффективностью грохочения. Вместе с тем при переработке углей повышенной влажности из-за налипания на валки и диски угольной мелочи эффективность работы грохотов снижается.
Недостатки валковых грохотов: большая масса, сложности конструкций, большой расход электроэнергии, сложность технического обслуживания.
2.5. Грохоты шнековые
Рабочая решетка шнековых грохотов типа ГШ состоит из системы валов-шнеков, размещенных параллельно один другому, и продольной оси грохота (рис. 2.6). Валы цилиндрической формы снабжены ребрами, расположенными по винтовой линии с постоянным шагом. При установке соседних валов по схеме «ребро против ребра» (рис. 2.7, а) образуется множество ячеек шестиугольной формы, которые при вращении валов-шнеков перемещаются к разгрузочному концу грохота, создавая «бегущую просеивающую решетку» с ячейками постоянных размеров. Образование ячеек предусмотрено для грохотов ГШ-500 и ГШ-1000. Для выделения из потока материала мелкой фракции 0–6 мм соседние валы-шнеки в грохоте ГШ-240 устанавливают по схеме «ребро входит во впадину между ребрами соседних валов-шнеков», в результате чего образуется щель грохочения (рис. 2.7, б).
Высокая производительность шнековых грохотов обеспечивается за счет принудительного перемещения исходного материала ребрами быстро вращающихся валов-шнеков по поверхности просеивающей решетки. При этом габариты ГШ невелики.
Рис. 2.6. Трехсекционный шнековый грохот ГШ1000
Грохоты отлично работают без залипания на влажном материале с включениями глинистых частиц, так как рабочий орган самоочищающийся. Высокая (до 95 %) эффективность грохочения обусловлена активным выпадением мелких частиц через ячейки или щели. Грохоты шнековые выполняются трехсекционными, в результате чего при перегрузке c одной секции на другую происходит взаимное перемещение частиц в потоке, что способствует лучшему выпадению мелочи в подрешетное пространство.
Большое распространение получил грохот ГШ-500, применяемый для отсева класса 0-13 мм на углеобогатительных фабриках. На одной из двух линий обогащения ГОФ «Капитальная» ПО «Интауголь» последовательно установленные грохоты ГИСЛ-82 и ГИСЛ-72 с ситами общей площадью 70 м, обеспечивавшие производительность 350 т/ч (простои на очистку сит составляли 30 % рабочего времени), были заменены одним грохотом ГШ-500 с рабочей решеткой площадью 9 м2. Это позволило увеличить производительность линии до 700 т/ч и в конечном итоге отказаться от строительства второй обогатительной фабрики. Срок окупаемости ГШ-500 не превышает 2 мес.
Рис. 2.7. Схема просеивающей решетки грохота шнекового ГШ:
а – с ячейкой просеивания; б – со щелью просеивания
2.6. Грохоты барабанные
Барабанные грохоты в зависимости от формы барабана могут быть цилиндрическими или коническими. Боковая поверхность грохота, образованная перфорированными, стальными листами или сеткой, является просеивающей поверхностью грохота.
Схема цилиндрического барабанного грохота показана на рис. 2.8, а Уголь подается внутрь барабана и благодаря вращению его поднимается на некоторую высоту, прижимаясь к стенкам барабана под действием составляющей силы тяжести и центробежной силы. Затем масса угля скатывается вниз. В этот момент вследствие наклона барабана происходит некоторое продольное перемещение угля от загрузочного к разгрузочному концу. После этого масса угля вновь поднимается, будучи прижата к внутренней стенке барабана, а затем скатывается вниз, одновременно продвигаясь вдоль барабана.
Траектория движения частиц в барабанном грохоте состоит из дуг окружности (при подъеме) и отрезков винтовой линии (при скатывании). Просеивание мелких частиц через отверстия сита происходит при скатывании угля вниз.
Для грохочения угля применяют конические барабанные грохоты с горизонтальным внутренним валом. Схема работы такого грохота понятна из рис. 2.8, б. Коническая форма барабана обусловливает при горизонтальной оси вращения его поступательное движение угля.
Рис. 2.8. Схемы барабанных грохотов
Барабанные грохоты могут изготовляться также для грохочения материала на несколько классов. При этом сито на барабане собирается по длине из нескольких секций с отверстиями, увеличивающимися в размерах по направлению к разгрузочному концу, т. е. грохочение материала производится от мелкого класса к крупному, или сита собираются концентрическими поверхностями – внутренние с наибольшими, а наружные с наименьшими отверстиями, т. е. грохочение производится от крупного класса к мелкому. В некоторых случаях применяются комбинированные конструкции, в которых на барабане, состоящем из нескольких секций сит с отверстиями, увеличивающимися в размерах, устанавливаются концентрически еще одно или несколько сит с мелкой сеткой.
Диаметр барабана колеблется от 500 до 3000 мм; длина – от 2000 до 9000 мм; длина отдельной секции барабана от 800 до 1500 мм.
Скорость вращения барабана ограничивается определенным пределом, так как при больших скоростях возникающая центробежная сила прижимает материал к рабочей поверхности и грохочение становится невозможным. Скорость вращения, при которой слой материала, прилегающий к поверхности барабана, начинает вращаться вместе с барабаном под действием центробежной силы, называется критической.
Критическая скорость вращения барабанного грохота
где R – радиус барабана, м.
Скорость вращения барабанных грохотов назначается меньше критической скорости в пределах:
Окружная скорость барабана поддерживается от 0,6 до 1,25 м/с.
Скорость движения материала вдоль оси барабана, т. е. скорость подачи, может быть определена по формуле:
где α – угол наклона барабана грохота, градус.
Теоретическая производительность по исходному материалу барабанного цилиндрического грохота, рассчитанная по транспортирующей способности его, при скорости подачи, определенной по формуле, равна %
где μ – коэффициент разрыхления материала, равный 0,6–0,8; γ – плотность материала, т/м3; h – толщина слоя материала на барабане (не более двойного размера максимальных кусков), м.
По практическим данным средняя производительность барабанного грохота составляет на 1 м2 площади сита и на 1 мм размера отверстий при сухом грохочении 0,25-0,3 т/ч, при мокром – около 0,45 т/ч.
ГП «Укрнииуглеобогащение» разработан и внедрен на многих шахтах и углеобогатительных фабриках цилиндрический барабанный грохот со спиральной просевающей поверхностью ГЦЛ (грохот цилиндрический легкого типа). Внешний вид этого грохота со снятым кожухом показан на рис. 2.9. Грохот состоит из цилиндра, свободно лежащего на катках, и привода (электродвигателя с редуктором), укрепленного на раме. Число заходов спирали составляет 12, 15 и 19 при размерах щели между витками 50, 70 или 100 мм. Грохот может принять куски, размером до 500 мм. Для предохранения спиралей от ударов поступающего угля имеется загрузочный конус-питатель. При вращении барабана надрешетный продукт перемещается спиралями к противоположному концу, подрешетный же проходит через щели между спиралями.
Рис. 2.9. Грохот барабанный со спиральными колосниками типа ГЦЛ:
1-электропривод; 2-питающая воронка; 3-колосники; 4-опорный бандаж; 5-приводной ролик; 6-рама
Основными недостатками барабанных грохотов являются их малая удельная производительность и низкая эффективность при грохочении мелкого материала. Это объясняется тем, что в каждый данный момент используется не более 20 % общей просеивающей поверхности грохота. Вследствие спокойной работы барабанного грохота и отсутствия встряхивания сита его отверстия легко забиваются зернами перерабатываемого материала.
От выше представленных барабанных грохотов выгодно отличаются появившиеся в последнее время барабанные классифицирующие устройства, рабочая поверхность которых формируется из резиновых динамически активных сит типа СДАЛ или эластичных сит типа ЭПП.
Важными достоинствами барабанных классифицирующих устройств являются: простота узлов и конструкций, плавности хода, низкая степень истирания грохотимого материала и динамическая активность элементов резиновых сит, способствующая самоочистки их ячеек.
Перечисленные качества позволяют широко использовать данный тип оборудования в технологических схемах обогатительных фабрик.
Научно-производственной фирмой «Размах» (г. Днепропетровск) создан целый типоразмерный ряд барабанных грохотов, общий вид одного из них схематично изображен на рис. 2.10.
Рис. 2.10. Общий вид барабанного грохота с ситом СДАЛ
В зависимости от технологических задач производства такие грохоты могут снабжаться самыми различными типами и комбинациями сит типа СДАЛ, обеспечивающими высокоэффективное сухое и мокрое грохочение по крупности от 300 до 0,3мм.
Рис. 2.11. Общий вид барабанного грохота с ситом ЭПП
ЗАО «АНА-ТЕМС» (г. Днепропетровск) создало и производит различные типы барабанных классифицирующих устройств с износостойкими резиновыми ситами ЭПП, для различных технологических операций, в т. ч. для сухого рассева сыпучих материалов по граничной крупности разделения от 6 до 50 мм.
На рис. 2.11 приведен общий вид барабанного грохота с ситами ЭПП.
2.7. Грохоты плоские качающиеся
Эти грохоты имеют один или два короба удлиненной прямоугольной формы с расположенными в них просеивающими поверхностями.
Короба устанавливаются на пружинных опорах или на шарнирных подвесках, совершая при этом с помощью привода кривошипного типа возвратно-поступательные круговые или сложные движения.
Одной из разновидностей такого типа грохотов с жесткой кинематикой является качающийся грохот с горизонтальным расположением сита, схематично изображенный на рис. 2.12.
Рис. 2.12. Схема горизонтального качающегося грохота:
1 – кривошипный привод; 2 – короб грохота; 3 – сито; 4 – опора; 5 – рама
Недостаток обычного кривошипного привода, применяемого для грохотов такого типа, – невозможность уравновешивания сил инерции качающихся масс, в результате чего на фундамент или на строительные конструкции передаются знакопеременные динамические нагрузки.
Вместе с тем быстроходные качающиеся грохоты типа БКГ в значительной мере лишены этого недостатка.
Конструкция грохота БКГ (рис. 2.13) состоит из рамы 1, двух коробов с ситами 2, шарнирных подвесок 3, шатунов 4, приводного вала 5, подвесок для вала 6, двух виброизолирующих пружин 7. Движение грохоту сообщается посредством ременной передачи от электродвигателя 8 через шкив 9.
Рис. 2.13. Общий вид быстроходного качающегося грохота типа БКГ
Исходный уголь поступает на верхний короб, надрешетный продукт транспортируется в сторону разгрузки, а из подрешетного продукта, попавшего на нижний короб, отсевается более мелкий класс.
Для уравновешивания возникающих при движении коробов динамических нагрузок эксцентрики шатунов расположены на валу на 180 градусов по отношению друг к другу, в связи, с чем короба движутся в разные стороны. Кроме того, вал грохота подвешен на подвесках и связан с виброизолирующими пружинами, поглощающими в немалой степени неуравновешенные динамические усилия. Подвески грохота соединены с коробами и рамой посредством шарниров, армированных резиной, что также смягчает удары, возникающие при работе грохота.
Характерным недостатком качающихся грохотов является наличие в их конструкциях большого количества шарнирных элементов и кривошипного привода, малоспособного обеспечить значительную по величине частоту колебаний, что необходимо для эффективного отсева мелких классов из рядовых углей и антрацитов при сухом грохочении. Поэтому в современных грохотах применяют преимущественно привод от вибровозбудителей.
2.8
Вибрационные грохоты с круговыми и
прямолинейными колебаниями
Эта группа инерционных виброгрохотов с дебалансным вибровозбудителем, принадлежащая к классу кинематически неопределенных грохотов. Различают вибрационные грохоты с круговыми и прямолинейными колебаниями короба.
На рис. 2.14 представлена кинематическая схема вибрационного грохота с круговыми колебаниями короба.
Рис. 2.14. Кинематическая схема вибрационного грохота с круговыми колебаниями
Короб грохота 4 с ситами 3 расположен на упругих виброизоляторах 2, смонтированных на опорной раме 1. В коробе грохота установлена труба 9, внутри которой проходит рабочий вал вибровозбудителя 10, вращающийся в подшипниках 8. На концах вала 10, имеющих эксцентричные расточки 7 радиуса r, насажены шкивы 5 с дебалансами 6, центр массы которых находится на расстоянии R от геометрической оси О1О2.
При вращении шкивов вокруг геометрической оси О1О2 возникает сила инерции массы короба M с материалом, Mˑω2ˑr которая уравновешивается равной ей по величине и противоположно направленной силой инерции дебалансных грузов (массой m) m ˑω2ˑR, где ω – угловая скорость вращения.
Из условия равенства упомянутых сил инерции и для частоты колебаний, далекой от резонанса, имеем:
В этом случае короб грохота описывает круговые колебания вокруг оси О1О2 , а сама ось вала остается в пространстве неподвижной, благодаря чему эти грохоты называются самоцентрирующимися.
Неподвижная ось рабочего вала и шкивов упрощает передачу им вращательного движения от электродвигателя и дает возможность применять короткую клиноременную передачу без риска сбрасывания ремней.
Инерционные грохоты типа ГИЛ
В инерционных грохотах ГИЛ с круговыми или близкими к ним колебаниям применяются в основном эластичные лепестковые муфты.
На углеобогатительных фабриках на операции сухого рассева углей грохоты типа ГИЛ получили широкое распространение.
На рис. 2.15 приведен общий вид грохота ГИЛ 52.
Рис. 2.15. Общий вид грохота ГИЛ 52
Конструкции грохотов типа ГИЛ аналогичны и имеют унифицированные узлы и детали. Грохот ГИЛ52 состоит из короба с просеивающей поверхностью, установленного или подвешенного на упругих виброизоляторах, инерционного вибровозбудителя, вмонтированного своими подшипниковыми узлами в боковинах короба, электропривода, соединенного с валом вибровозбудителя эластичной муфтой.
Короб представляет собой пространственную рамную металлоконструкцию, включающую две вертикальные несущие боковины, соединенные между собой одним или несколькими рядами поперечных горизонтальных связь-балок круглого или прямоугольного сечения. Число явно выраженных рядов поперечных связь-балок определяется количеством ярусов (дек) сит грохота. При сборке короба практически, все унифицированные узлы крепятся высокопрочными болтами.
В настоящее время многие отечественные фирмы освоили изготовление инерционных виброгрохотов по индивидуальным заказам потребителей в соответствии с их техническим заданием.
ООО «ЛЭМЗ» (Украина) разработано и осваивает серийное производство более эффективных виброгрохотов с эллиптическими колебаниями типа ГВИ с перспективной последовательной замены грохотов ГИЛ на углеобогатительных фабриках в узлах сухого подготовительного грохочения.
Общий вид грохота типа ГВИ приведен на рис. 2.16.
Рис. 2.16. Общий вид грохота типа ГВИ
Если одновальные грохоты типа ГИЛ с вибровозбудителями, расположенными в центре масс, имеют практически одинаковые колебания по всей длине рабочей поверхности близкие к круговым, то грохоты типа ГВИ имеют неоднородное поле эллиптических амплитуд колебаний.
Неоднородные поля эллиптических амплитуд в разработанных и созданных ООО «ЛЭМЗ» грохотах типа ГВИ (ГВИ52С, ГВИ62ЛС, ГВИ72ЛС и т. п.) для сухой классификации сыпучих материалов (уголь, известняки, руды, стройматериалы) создаются расположением одновальных вибровозбудителей на периферии боковин в определенном месте относительно центра масс грохота, за счет чего формируется оптимальное для каждого вида грохотимого материала поле эллиптических амплитуд, изменяющихся как по величине, так и по направлению при движении от загрузки к разгрузке.
Установка такого типа грохотов под углом от 12° до 25° и регулирование величины амплитуды центра масс грохота позволяет добиваться более высокой эффективности при требуемой производительности по исходному питанию, чем на грохотах традиционных конструкций. Это подтверждает опыт эксплуатации грохотов с шириной дек от 2,0 м до 2,4 м и площадями рабочих поверхностей от 9 до 13 м2 на различных операциях сухого грохочения известняка на ДОФ-3 ОАО «Стагдок» (г. Липецк, Россия), который позволяет с уверенностью утверждать о перспективности грохочения сухих сыпучих материалов на грохотах с неоднородным полем эллиптических колебаний.
Инерционные грохоты типа ГИТ
Для предварительного грохочения применяются инерционные грохоты тяжелого типа ГИТ51А и ГИТ71.
По принципиальной схеме работы грохоты типа ГИТ подобны грохотам типа ГИЛ и состоят из аналогичных сборочных единиц, но имеют некоторые конструктивные отличия, связанные со спецификой назначения.
Грохот ГИТ51А в опорном (рис. 2.17, а) и подвесном (рис. 2.17, б) исполнениях является наиболее надежным из инерционных грохотов, так как его короб и просеивающая поверхность изготовляются из толстолистового проката, а детали короба соединяются высокопрочными болтами. Массивность элементов конструкции короба определяется не только требованиями надежности, но и динамикой грохота. Значительно большая масса короба грохота ГИТ51А по сравнению с массой короба грохота ГИЛ52 при меньшей площади просеивающей поверхности обеспечивает стабильность амплитуды колебаний короба даже тогда, когда на его просеивающей поверхности находится несколько кусков грохотимого материала большой массы (допускаются куски размером до 1200 мм).
Рис. 2.17. Грохот ГИТ51А в опорном (а) и подвесном (б) исполнениях
Короб грохота изготовляется из двух высоких боковин 1 толщиной 12 мм с накладными листами в местах крепления вибратора 2, поперечных связей швеллерного профиля, подситных рам и защитных листов, предохраняющих боковин от истирания. Короб имеет одну просеивающую поверхность 3 из двух карт, закрепленных в коробе болтами. В середине короба часть просеивающей поверхности отверстий не имеет. Под этой частью расположен вибратор, и благодаря отсутствию отверстий он не подвергается абразивному износу. Просеивающая поверхность представляет собой листовое решето толщиной 25 мм с квадратными отверстиями. Для предохранения от интенсивного износа на лист наварены продольные брусья сечением 40×40 мм, которые по мере износа заменяются.
Конструкция короба предусматривает возможность установки колосниковой просеивающей поверхности из отдельных секций, устанавливаемых каскадом. При этом щель расширяется к концу секции.
Грохоты самобалансные типа ГСЛ
По принципу действия самобалансный грохот является инерционным, но благодаря особому вибратору обладает преимуществом резонансного грохота – горизонтальным расположением просеивающей поверхности. Самобалансный грохот имеет преимущества как инерционных (простота конструкции и отсутствие необходимости в периодической настройке), так и резонансных (удобство компоновки, пригодность для процессов обезвоживания) грохотов. Угол подбрасывания материала у этого грохота больше, чем у резонансного, что обеспечивает более эффективное отделение воды. Самобалансный грохот передает на опору меньшие динамические нагрузки, чем резонансный.
Промышленностью выпускается три типоразмера самобалансных грохотов: ГСЛ42, ГСЛ62 и ГСЛ72.
Грохоты типа ГСЛ предназначены для мокрой классификации углей, антрацитов и горючих сланцев, обезвоживания продуктов обогащения, отделения шлама, отмывки утяжелителя.
Самобалансный грохот ГСЛ62 (рис. 2.18) состоит из короба 5 с просеивающими поверхностями, инерционного вибратора 1, пружинных опор или подвесок 4, электродвигателя 3 и клиноременной передачи 2.
Рис. 2.18. Грохот ГСЛ62
В отличие от инерционного наклонного грохота здесь применяется самобалансный вибратор, в корпусе которого на параллельных валах размещены два цилиндрических зубчатых колеса и одинаковые дебалансы. Колеса имеют равное число зубьев, благодаря чему валы вращаются с одной угловой скоростью в противоположные стороны. Дебалансы расположены по отношению друг к другу так, что при вращении валов результирующая их центробежных сил изменяется по синусоиде и всегда действует по оси, проходящей через центр тяжести короба, вызывая его колебания.
Короб движется практически поступательно: все его точки колеблются в вертикальных плоскостях, перпендикулярных осям валов вибратора, по прямолинейным траекториям под углом к плоскости просеивающей поверхности. При этом материал, находящийся на просеивающей поверхности, подбрасывается и просеивается.
Конструкция грохота ГСЛ72 (рис. 2.19) в основном не отличается от конструкции грохотов ГСЛ42 и ГСЛ62. Разница лишь в том, что в связи с большими размерами он имеет шесть пружинных опор и два спаренных самобалансных вибратора, установленных на специальных площадках над боковинами короба. Вибраторы приводятся в действие соответственно двумя электродвигателями, помещенными на отдельных рамах.
Рис. 2.19. Грохот ГСЛ72
Самобалансные вибраторы грохота такие, как и у грохотов ГСЛ42 и ГСЛ62, соединены между собой промежуточным валом с муфтами.
Грохот ГСЛ72 выпускается только в опорном исполнении.
На базе грохотов ГСЛ42, ГСЛ62 и ГСЛ72 с использованием их основных узлов и элементов созданы грохоты ГСЛ82 и ГСЛ91 с полезной площадью просеивающей поверхности, соответственно, 21 м2 и 33,2 м2.
Грохоты резонансные типа ГРЛ, ГРД
Грохоты типа ГРЛ и ГРД предназначены для подготовительной и окончательной сухой и мокрой классификации углей, обезвоживания продуктов обогащения, отделения циркуляционной суспензии, обесшламливания, отмывки утяжелителя. В зависимости от назначения грохот комплектуется просеивающей поверхностью соответствующей конструкции с отверстиями необходимых размеров и формы.
По принципу действия и конструкции грохоты представляют собой двухмассные динамические колебательные системы с упругими связями между массами и эффективной виброизоляцией. Нелинейная характеристика жесткости упругих связей благодаря применению резиновых буферов на 30 % повышает ускорение короба (и просеивающей поверхности) по сравнению с качающимися грохотами. При одинаковом с качающимися грохотами характере колебаний короба интенсивность грохочения у резонансных выше благодаря как нелинейности упругих связей, так и большей частоте колебаний. Работа в режиме, близком к резонансному, обеспечивает возможность колебаний коробов больших размера и массы при минимальных затратах энергии и минимальных нагрузках на детали привода. Эти грохоты наиболее производительны и универсальны по назначению. Однако им присущи недостатки, основные из которых – сравнительная сложность в эксплуатации и большая масса.
Промышленностью выпускаются два типа резонансных грохотов – ГРЛ и ГРД. Принципиальные конструктивные схемы этих грохотов различны. ГРЛ – грохот резонансный легкого типа с одним коробом и уравновешивающей подвижной рамой. ГРД – грохот резонансный двухкоробный без уравновешивающей рамы.
Грохот ГРЛ (рис. 2.20) представляет собой колебательную систему двух масс (короба 4 с просеивающими поверхностями и подвижной рамы 1), связанных между собой системой упругих связей: плоскими рессорами 5, пружинными опорами 6, буферами 7, укрепленными как на коробе, так и на раме. Рама установлена на амортизаторах 8. При наклонном расположении грохота применяются поддерживающие пружины 9. Привод 2 кривошипно-шатунного типа установлен на раме с загрузочной стороны короба. Вал приводится во вращение от электродвигателя 10 посредством клиноременной передачи 11. Шатун привода с помощью резиновых элементов 3 упруго соединяется с коробом, благодаря чему привод не нагружается большими инерционными силами движущихся масс и большие пусковые нагрузки устраняются. Буфера установлены с зазором суммарной амплитуды колебаний короба и рамы. Это определяет нелинейный характер упругих связей между коробом и рамой. Плоские рессоры обеспечивают направленные колебания короба и рамы под углом α к плоскости просеивающей поверхности. Амортизаторы 8 и 9 обеспечивают возможность колебаний рамы и при этом передают на опору грохота динамические нагрузки, намного меньшие сил инерции подвижных частей грохота. Расположение центров тяжести короба и рамы на прямой АВ, параллельной осям буферов и перпендикулярной рессорам, позволяет осуществлять при колебаниях возвратно-поступательное движение короба и рамы.
Рис. 2.20. Принципиальная схема двухмассного резонансного грохота типа ГРЛ
При вращении вала привода, имеющего эксцентриситет, происходит деформация приводных упругих связей по закону, близкому к гармоническому. Периодически изменяющаяся сила упругости резиновых элементов привода представляет собой возмущающую силу, вызывающую вынужденные колебания короба и рамы. Рабочая частота вынужденных колебаний системы принимается близкой к резонансной.
Колебания короба и рамы происходят навстречу друг другу поэтому сила инерции от движения массы короба гасится противоположно направленной силой инерции массы рамы. Масса рамы грохота в 1,5–3 раза тяжелее короба, соответственно и амплитуда ее колебаний во столько же меньше амплитуды колебаний короба.
Грохоты типа ГРД (рис. 2.21) отличаются от грохотов с уравновешивающей рамой наличием короба вместо рамы. Коробы (верхний 1 и нижний 2), имея одинаковую массу, колеблются с одинаковой амплитудой. Центры тяжести коробов, как и в грохотах типа ГРЛ, находятся на одной прямой, параллельной оси нелинейной упругой связи. Благодаря замене уравновешивающей рамы коробом грохот имеет почти в два раза меньшую массу и меньшие габаритные размеры при тех же площадях просеивающей поверхности, а наличие равноплечих рычагов 3 с центральными осями исключает необходимость применения пружинных опор короба и продольных опор грохота. Наклон коробов достигается более высоким расположением оси рычагов с загрузочной стороны грохота, чем ось рычагов с разгрузочной стороны.
Отсутствие линейных упругих связей между коробами в грохоте ГРД (пружин и рессор) при прочих одинаковых условиях обеспечивает большую нелинейность системы, но вместе с тем обусловливает большие боковые колебания, чем в грохоте типа ГРЛ.
Рис. 2.21. Грохот типа ГРД
Резонансные грохоты по сравнению с грохотами других типов, в частности с инерционными, имеют ряд преимуществ:
горизонтальное расположение, обусловливающее минимальные габаритные размеры здания;
наличие упругой связи привода, благодаря которой нагрузки на узлы привода при запуске грохота минимальны;
нелинейность упругих связей между коробами, что создает интенсивный режим встряхивания грохотимого материала на просеивающей поверхности и, следовательно, высокую эффективность грохочения;
режим колебаний масс грохота, близкий к резонансному, в силу чего расход мощности на приведение в колебание сравнительно больших масс грохота и грохотимого материала минимален;
универсальность применения (как на сухих, так и на мокрых операциях грохочения);
малая чувствительность к перегрузкам при установившемся режиме колебаний;
малые динамические нагрузки на опоры (у грохотов типа ГРД).
Наряду с перечисленными преимуществами резонансные грохоты имеют и существенные недостатки, которые в настоящее время ограничивают область их применения. К таким недостаткам относятся, в первую очередь, сложность изготовления (особенно грохотов типа ГРД) и значительные трудности при эксплуатации. Наличие в грохотах упругих связей, пружинных опор и рессорных подвесок требует квалифицированного монтажа и обслуживания, своевременного профилактического ремонта, что редко обеспечивается при эксплуатации грохотов. Другой недостаток грохотов – сравнительно большая масса, особенно у грохотов типа ГРЛ. Попытка использования грохотов типа ГРД для мокрой классификации показала их крайне низкую эксплуатационную надежность и, следовательно, нецелесообразность применения на этой операции.
Грохоты самобалансные с самосинхронизирующимися вибровозбудителями типа ГИСЛ
В настоящее время в угольной и горнорудной промышленности наибольшее применение находят инерционные (самобалансные) грохоты с прямолинейными колебаниями короба, как наиболее простые в изготовлении, эксплуатации и ремонте.
Существенным недостатком самобалансного грохота с двухвальным вибровозбудителем является наличие зубчатой передачи, создающей сильный шум и требующий частого ремонта. Он устранен в самосинхронизирующемся грохоте, имеющем два независимых дебалансовых вибровозбудителя, непосредственно не связанных между собой какой-либо передачей. Их валы вращаются отдельными электродвигателями в противоположном направлении с одной и той же угловой скоростью (+w и – w) и с одной и той же фазой, благодаря автоматической самосинхронизации и самофазировке, достигаемой путем соответствующего подбора движущихся масс, их моментов инерции и взаимного расположения. Такого рода вибровозбудители являются самосинхронизирующимися. Их валы с дебалансными грузами, закрепленные в бортовых стенках короба, вращаются навстречу друг другу, поэтому результирующая центробежных сил инерции направлена по прямой АА и проходит через центр массы короба. В результате достигаются прямолинейные синусоидальные колебания под заданным углом к плоскости сита.
Грохот типа ГИСЛ обладает преимуществами как резонансного грохота (горизонтальное расположение просеивающей поверхности, колеблющейся возвратно-поступательно под углом 45° к горизонту), так и инерционного (прост в изготовлении и удобен в эксплуатации, так как не требует никаких регулировок). В отношении конструктивного исполнения и кинематической схемы грохот типа ГИСЛ аналогичен самобалансному грохоту типа ГСЛ.
Вся практика проектирования и разработки грохотов до настоящего времени характеризовалась попыткой внедрения универсальных грохотов. Однако накопленный опыт показывает, что сухое грохочение большинства сыпучих материалов более эффективно при круговых или близких к круговым колебаниям рабочих поверхностей грохотов, мокрое же грохочение (классификация, обесшламливание, отделение суспензий, обезвоживание и т. п.) более эффективно при направленных колебаниях, создаваемых инерционными силами вибровозбудителей под определенными углами относительно рабочей поверхности.
Поэтому на углеобогатительных фабриках на операции сухого рассева рядовых углей использование самобалансовых грохотов типа ГИСЛ малоэффективно. Вместе с тем при разделении рядовых углей по граничной крупности свыше 13 мм эти грохоты могут работать удовлетворительно.
Общий вид грохота ГИСЛ 62 показан на рис. 2.22.
Рис. 2.22. Общий вид грохота ГИСЛ-62
Короб грохота 1, установленный на четырех пружинных опорах 2, совершает направленные колебательные движения в вертикальной плоскости под действием центробежной силы инерции, возникающей при вращении в противоположные стороны дебалансовых грузов, установленных на двух параллельных валах вибровозбудителя 3. Траектория движения точки короба представляет собой прямую линию, наклоненную в данном случае под углом 45 градусов к плоскости сита 4. Вращение валам вибровозбудителя передается двумя двигателями 5 через эластичные лепестковые муфты 6.
Короб состоит из двух боковых листов (боковин) толщиной 8 мм, поперечных связь-балок, изготовленных из труб круглого сечения, и балки в загрузочной части короба. Поперечные связь-балки закрыты резиной, которая предохраняет их от абразивного изнашивания. Боковые короба усилены листами, угольниками и швеллерами в продольном и вертикальном направлениях. Для установки короба на опорах к боковинам прикреплены цапфы 7. Внутри короба вдоль боковых листов прикреплены угольники, на полки которых устанавливаются рамки верхнего сита. Нижние поперечные связь-балки связывают посредством высокопрочных болтов боковины, образуя пространственную форму короба, и служат также опорами для нижнего сита.
На коробе грохота установлен самосинхронизирующийся вибровозбудитель, состоящий из корпуса, внутри которого на подшипниках качения размещены параллельно друг к другу валы с неуравновешенными дебалансами.
Грохоты высокочастотные
Основным направлением интенсификации и повышения точности разделения при сухом и мокром грохочении, обезвоживании, обезшламливании и отмыве суспензии от продуктов обогащения при создании современных грохотов является повышение их вибродинамических характеристик.